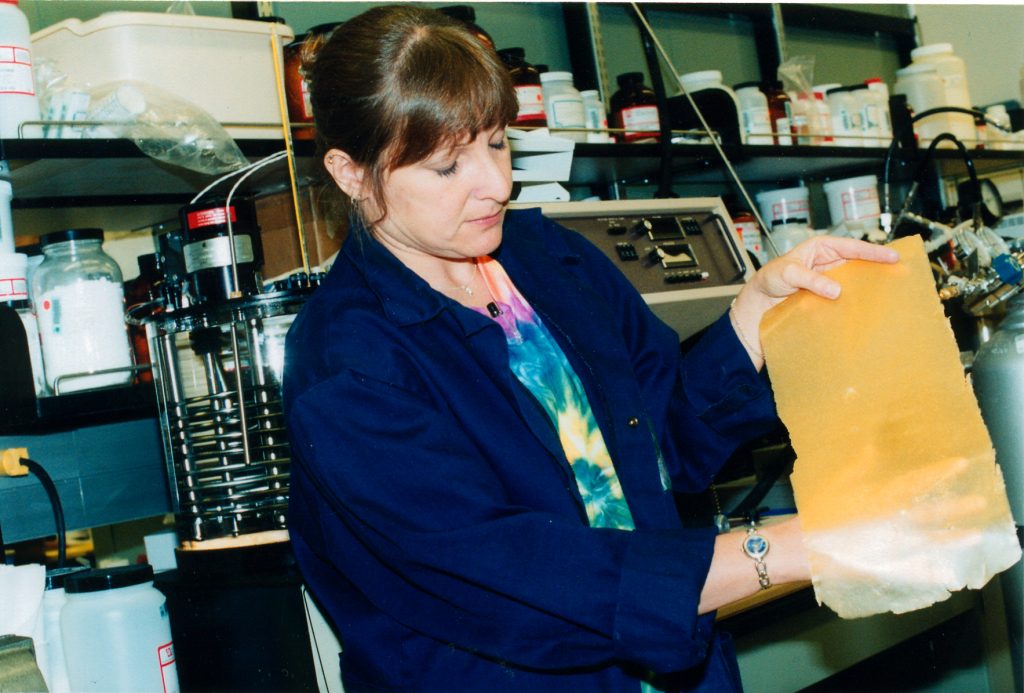
Download 300dpi JPEG image, ‘adhesive1.jpg’, 1.8MB (Media are welcome to download/publish this image with related news stories.)
ALBUQUERQUE, N.M. — A Sandia National Laboratories research team, led by scientist Jim Aubert, has developed a removable epoxy adhesive that makes bonding and detaching parts a matter of temperature change.
“Our approach to a removable adhesive relies on the use of a reversible chemistry that breaks apart the adhesive at elevated temperatures, resulting in low adhesive molecular weight and low bond strength,” Aubert says.
Sandia is a Department of Energy National Laboratory.
No other adhesive with the strong bonding characteristics of an epoxy has the capability of melting — becoming liquid — and losing its bonding capability at high temperatures and then rebonding when the temperature is lowered.
Conventional adhesives become soft at high temperatures, but do not melt and do not lose their ability to bond. Thus, to detach two objects, they must be pried apart, which can cause damage.
The bond in the Sandia adhesive breaks at 90 to 130 degrees C (roughly 190 to 260 F) depending on the formulation. Minimal force is then required to separate the pieces at this heated state. The adhesive will rebond between room temperature (about 20 to 25 C) and 60 C.
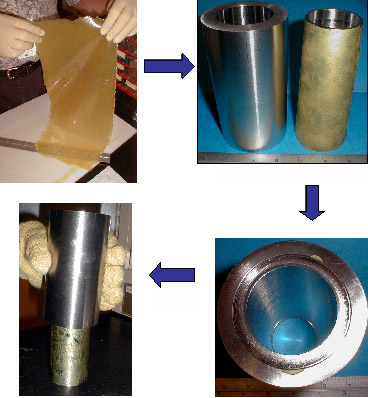
Download 72dpi JPEG image, ‘adhesivesequence.jpg’, 76K (Media are welcome to download/publish this image with related news stories.)
Aubert notes, however, that this rebonding capability is finite. The adhesive will retain the ability to bond and unbond a number of times but will at some point become nonremovable.
The relatively low debonding temperature makes for versatile component assembly, easier and cheaper component repair, easy upgrading, and simplified dismantlement and recycling. It allows for upgrading as new technology becomes available or rebuilding if any defects are discovered after deployment or during the original manufacturing.
“Normally, no thought is given to disassembly after bonding parts with an epoxy,” Aubert says. “Yet disassembly is becoming an increasingly important aspect of manufacturing as we become more concerned with the cradle-to-grave aspect of materials for environmental and economic reasons.”
For example, future weapon systems are planned that can be taken apart periodically for repair and upgrades. Removable adhesives are critical for this type of component disassembly and reassembly.
Aubert says the new adhesive might also be useful for components that need to be put together, tested, and then taken apart for analysis.
The unheated adhesive looks and feels like a large rubber band, having an elastic quality. It can be prepared in any size and thickness. For bonding, it is cut to match objects being attached, applied to one surface, and melted. The bond is made by bringing the melted adhesive into contact with the other surface and curing it between room temperature and 60 degrees C. The adhesive then can be removed at 90 to 130 degrees C, with the adhesive liquefying at different temperatures for different formulations.
The removable adhesive has been successfully applied to numerous metals and to some foams and polymers. This research is part of a larger ongoing team effort in Sandia’s Materials and Process Sciences Center, which previously developed removable encapsulants and is working on removable conformal coatings. Conformal coatings are applied to circuit boards to provide protection from the environment, mainly moisture, debris, and chemicals. They are usually thin and ideally coat everything on the board evenly. To rework a board, the coating is removed — hence the removable conformal coating.
Sandia Technical contact:
Jim Aubert, jhauber@sandia.gov, (505) 844-4481