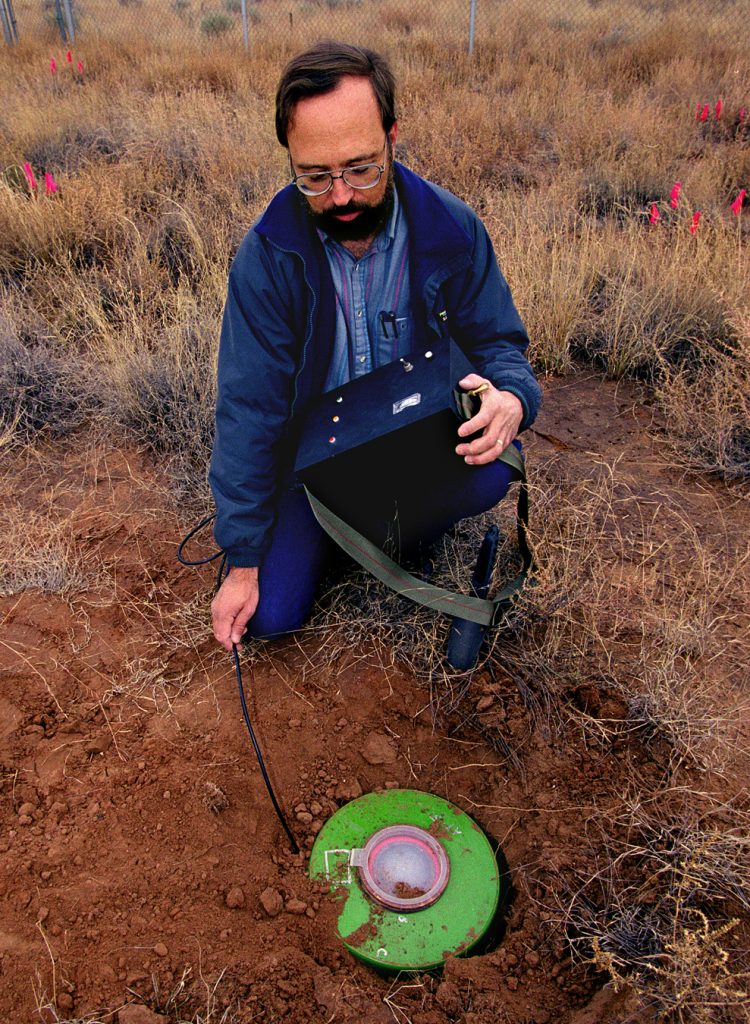
ALBUQUERQUE, N.M. — Sandia National Laboratories has joined the effort to rid the planet of what some people have called its worst form of pollution — land mines.
Sandia’s work in land-mine detection and demining ranges from chemical sensing and backscattered x-ray technologies, to laying down quick-hardening foam to clear a path for military vehicles. Sandia, a Department of Energy (DOE) national security laboratory, also is developing robotic vehicles that can be used as platforms to support the technologies.
There are three levels of demining. The first is standard military demining used for clearing a path for soldiers and vehicles during war. Speed counts, and some casualties are expected. The second also is connected to military operations and deals with an army’s need to clear greater numbers of mines in an occupied country. This is similar to the case of the United Nations’ occupying forces in Bosnia-Herzegovina. The third is humanitarian demining, which is the removal of all mines from an area and its restoration to productive use.
Ron Woodfin, who oversees Sandia’s demining efforts and who has represented the labs at several international conferences on demining, says the consensus is there is no “silver bullet,” or one technology that can unfailingly detect all types of mines under all types of conditions.
Current state-of-the-art demining technologies are mostly various forms of anomaly detectors, or those that detect things not expected in their environments. The detectors include passive infrared, microwave, electrical conductivity, and ground-penetrating radar, but they so far have shown to be very expensive, have low accuracy, and a high false-alarm rate. Metal detectors are the most prevalent form of electronic mine detection, but are largely ineffective for some of today’s plastic mines. And like all anomaly detectors, metal detectors give high rates of false alarms in battle zones filled with bullet casings and other metal debris. Brute force methods using plows, rakes and explosive breaching are sometimes used to clear a path for soldiers and vehicles, but almost always fail to find or detonate all mines. The most reliable method of mine clearing, but also the slowest and most dangerous, is manually probing the soil with a rod.
Worldwide, there are an estimated 100 million land mines throughout 68 countries. Those with the worst problem are Angola, Afghanistan, Cambodia, Iraq, Laos and Bosnia-Herzegovina.
Each year an estimated 100,000 mines worldwide are cleared, but another 2 million are laid. An average of 2,000 people each month are killed or maimed by land mines.
“Even if everyone stopped laying mines today, it still would take 1,000 years to clear those now in the ground throughout the world,” says Woodfin of the Electronic Fuzing Department. “In my mind, it’s the worst form of pollution mankind has ever come with, bar none.”
Chemical Sensing
One of the most promising technologies under development at Sandia to identify sea mines, land mines, and unexploded ordnance is chemical sensing. All mines apparently emit explosive molecules. Sandia is helping to develop a portable system that incorporates ion mobility spectrometry (IMS) — the same technology developed for the explosives-detection portal to check airline passengers — that will be capable of quickly detecting and classifying minute quantities of explosive molecules. The system is not an anomaly detector since it looks for the explosive molecules themselves rather than a container holding the explosives. It incorporates a new Sandia-developed concentration technology, which potentially can chemically amplify the source strength thousands of times.
The project originally was directed at detecting sea mines and unexploded ordnance in shallow water and is sponsored jointly by the DOE and Department of Defense, Office of Munitions. Many land mines actually are placed in water such as rice paddies, fords, and domestic water sources, laundry areas and irrigation canals. That work, which is ongoing, has since been expanded to land mine detection with the help of Defense Advanced Research Projects Agency (DARPA) funding and Laboratory Directed Research and Development (LDRD) funds.
“We are the world leader by a nose in the area of chemical sensing for explosive classification, and we will be able to demonstrate that soundly in the next six months,” says Woodfin, who has worked closely on the project with numerous Sandians in a cross-section of disciplines.
Jim Phelan of Sandia’s Environmental Restoration Technology Department and Steve Webb of the Mission Analysis and Simulation Department are supporting development of the land mine chemical sensing technology by modeling the environmental fate and transport (EF&T) of explosive signature molecules. They are analyzing how environmental conditions such as temperature and precipitation influence the movement of explosive molecules through soil, air, and water.
“What this work will emphasize is the significant influence of environmental conditions, such as temperature, soil type, precipitation and evaporation on the movement of chemical signature molecules to locations that can be detected by the chemical detector,” Phelan says. “For instance, the amount of explosive signature molecules emitted from a mine in Bosnia may show a much different concentration at the ground surface than a mine in Iraq or Afghanistan. We’ll also evaluate such things as whether it’s better to look for mines in the afternoon when soil is warmer rather than during the morning, and how rainfall affects detection.”
Phil Rodacy of the Explosives Materials/Subsystems Department and Bill Chambers of the Analytical Chemistry Department have been doing much of the field work related to the development of the chemical sensor technology. They periodically take soil samples from a small mock minefield inside a fenced area at Sandia. The minefield has six unfuzed antitank mines and several surrogate mines made of plastic or consisting of metal boxes painted with explosive compounds. They also plan to conduct field tests on small, antipersonnel mines.
Rodacy and Chambers periodically analyze soil samples to determine the concentration of explosive molecules that can be found at various distances from the mines. They also have taken samples in shallow water for the chemical detection of unexploded ordnance (UXO). Both water and soil pose different challenges, they say. Explosives dissolve easily in water, making it difficult to extract the explosive molecules. Water also is often a dirty environment, with salts, organic materials and pollution interfering with the process. Soil also has interfering chemicals, and environmental factors such as moisture and temperature can affect the performance of the technology.
The IMS technology already has successfully analyzed both water and soil field samples in the laboratory at the Explosives Components Facility. The technology also was successfully demonstrated in the field on San Clemente Island as part of a two-year program with the Office of Naval Research. The key now is to reduce the technology to the portable stage, which has been aided by a new IMS designed and developed by Electronic Research Group in Las Cruces and based on work done at New Mexico State University.
Woodfin estimates a portable system weighing no more than 20 pounds will be ready to field test for sea mines by next spring. The system probably will have a sensing tube that extends from a box and will be simple to use: A green light will indicate the unit is sampling but has found no explosives; a yellow light will mean a small concentration of explosives has been found and that further sampling is required; and a red light will indicate a significant concentration of explosive has been detected.
Rodacy said if the water field test goes well in the spring, the technology should be in use by the military and available for licensing within another year. The soil IMS system probably will be ready for field use a year or two after that.
“We want to get this down to what one person can carry reasonably comfortably, and which ultimately could be put on some robotic crawler of some sort,” says Chambers. “The push is really to scale this down to a rugged, lightweight package for the field.”
Development of a miniaturized mine detector is one of the applications of a wider Grand Challenge LDRD Proposal to develop an autonomous micro-scale chemical laboratory, more commonly called “�ChemLab.” Greg Frye of the Microsensor R&D Department says Sandia’s microfabrication capabilities are being used to develop chemical sensing modules the size of a postage stamp that will be used to make micro-chemical-analysis systems the size of current palm tops. The systems will have unprecedented capabilities for sensitively detecting and deciphering detailed chemical signatures, and will have a wide variety of uses in areas such as covert sensing for nonproliferation, contraband and land-mine detection, medical diagnostics, and environmental and process monitoring.
Backscattered x-rays
Sandia is receiving funding from the U.S. Army as well as the DoD/DOE Memorandum of Understanding managed by Tom Hitchcock of Sandia’s Joint Department of Defense/Department of Energy Munitions Technology Department to help develop a mobile, continuously scanning, x-ray machine that can detect mines. Steven Shope, project manager of the backscattered x-ray project, says the technology in September successfully imaged antitank mines buried in sand and rocky New Mexico soil. The image showed enough detail to ascertain the type of mine and the location of its fuse, which is important for unearthing it.
“This was the first time this technique had been demonstrated in the field,” says Shope, who has worked on the project with Grant Lockwood of the Materials Radiation Science Department. “It’s the only process that gives a real-time image of a buried mine.”
Development of a field-ready prototype, however, is still about a year away, and it could be another year after that until the backscattered x-ray mine detector is in actual use.
The continuously scanning, x-ray machine itself was designed and fabricated by Imatron Inc. under contract to the U.S. Army’s Night Vision and Electromagnetic Sensors Directorate (NVESD) at Fort Belvoir, Va. Sandia was contracted by NVESD to prepare the x-ray unit for field tests, to integrate Sandia-developed detector technology, and to integrate imaging algorithms developed by the University of Florida into a fieldable land-mine detector.
The technique relies on the absorption and scattering of energetic photons. A detector system located above the soil intercepts backscattered photons. A higher detector response is recorded when the beam strikes a plastic land mine than when it strikes only soil. Other materials in the soil, such as organic matter and rocks, can also create the higher detector response. To avoid false alarms, a microprocessor produces a visual real-time image for immediate observation and analysis.
For the recent field test, the experimental backscatter x-ray imaging system was suspended from a gantry that rolled on small, movable tracks above a small field in which several antitank and antipersonnel mines had been buried. The information was sent to a computer situated in a van near the field.
“The system can image land mines down to about four inches through water and snow, and all types of debris such as rocks, logs, and leaves,” says Shope of the Electromagnetic Propulsion/Beams Applications Department. “It can image one square meter in about five minutes.”
Shope says now that the technology has been successfully demonstrated in a field test, the next step is to produce a prototype system that probably will go into a redesigned Humvee. An ideal platform for the detector system itself, Steve says, probably would be the Remote TeleRobotic Vehicle for Intelligent Remediation (RETRVIR), an all-terrain vehicle that has a robotic arm that can dig and pick up objects weighing up to 250 pounds.
Foam Countermine Development
Woodfin also is project manager and principal investigator for another MOU-sponsored project to determine the effectiveness of rigid polyurethane foam to neutralize mines and barriers. Several field tests have already been conducted to determine the effectiveness of quick-hardening foam to serve as a cushion against land- and water-mine explosions for vehicles and soldiers. The foam has successfully withstood the weight of trucks and tanks. Although the field tests so far have shown the foam is adequate from the standpoints of wear and strength, further work and tests are continuing, including explosive experiments in air, soil, and water, Woodfin says.
Sandia is a multiprogram DOE laboratory, operated by a subsidiary of Lockheed Martin Corp. With main facilities in Albuquerque, N.M., and Livermore, Calif., Sandia has major research and development responsibilities in national security, energy, and environmental technologies and economic competitiveness.
Technical contact:
Ron Woodfin, rlwoodf@sandia.gov, (505) 844-3111