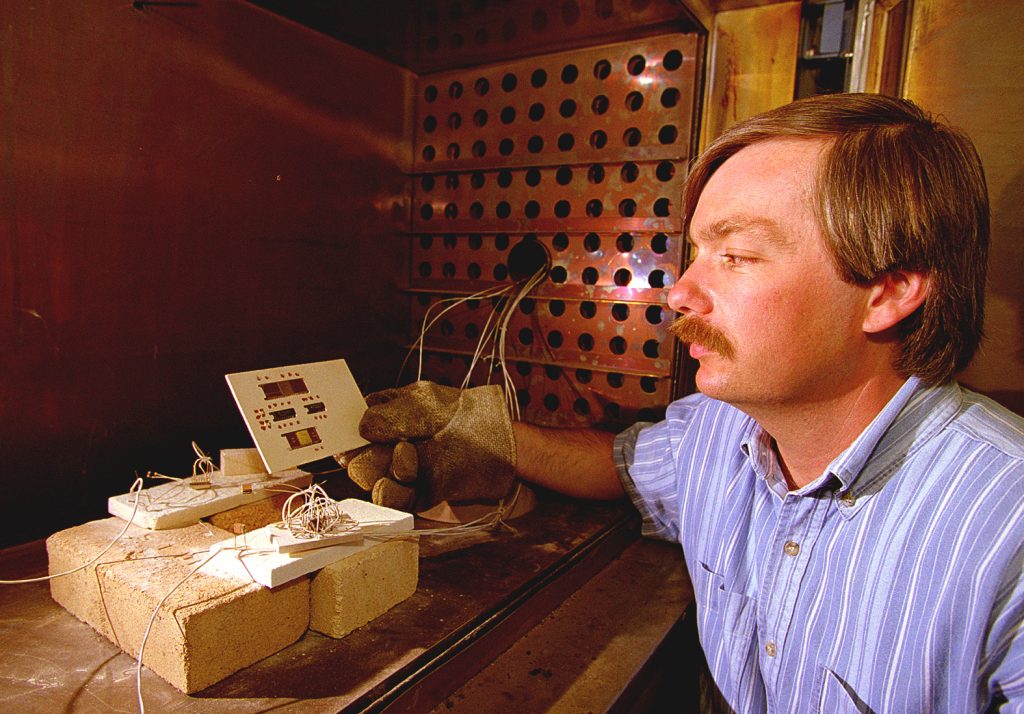
Download 150dpi JPEG image, ‘GeoOven.jpg’, 1.6MB
ALBUQUERQUE, N.M. — Research under way in Sandia National Laboratories’ Geothermal Research Department may improve the economic feasibility of using geothermal energy — water heated deep inside the earth’s crust — to produce electricity.
“Right now less than three percent of electricity in the U.S. comes from geothermal energy because it costs twice as much to produce as electricity created from natural gas. Our work at Sandia could help change that,” says Randy Normann, project principal investigator.
He and colleague Joseph Henfling are experimenting with Honeywell silicon-on-insulator (SOI) electronics and evaluating and designing new electronic instrument systems operating at up to 315 degrees C. That is more than 100 degrees hotter than systems presently available to the geothermal industry.
“The industry views this as a quantum leap,” Normann says.
The Sandia project is funded by the Department of Energy Office of Geothermal Technologies.
Research may change way industry solves problems
Normann notes that using electronics that can withstand high temperatures is important because the research may allow the geothermal industry to start changing the way it solves certain problems. For example, geothermal wells account for approximately one-fourth to one-half the cost of a geothermal power plant. Geothermal wells are expensive, partly due to the rock formations and high drilling temperatures. In addition to well cost is drilling uncertainty. Even within known producing reservoirs, the driller often fails to hit a fluid-producing fracture. With new high-temperature electronics, drillers can deploy guidance tools behind the drill bit to steer the drilling process, reducing drilling time and risk.
At present, electronics and batteries used in geothermal well applications must be encased in a Dewar flask, which Normann describes as a “big Thermos bottle” made of evacuated double-walled steel. Temperatures in the geothermal wells can be as high as 350 degrees C, much too hot for standard electronics to function properly without the protection of Dewars.
However, the Dewar only buys time within the well before equalizing in temperature, about 10 hours.
“Every time one of these Dewared instruments is pulled out of the well during drilling, it costs $8,000 to $10,000, ultimately increasing the cost of geothermal energy,” Normann notes.
He adds that, “In general, all circuit components exist today for high-temperature use up to 200 degrees C. This temperature is too low for most geothermal applications, which require instrumentation capable of operation at up to 300 degrees C with high reliability. This covers about 90 percent of the geothermal industry,” Norman says.
Instruments used in geothermal applications must be able to bear high temperatures or be placed in the protective Dewars because geothermal energy originates in the earth’s interior where the hottest fluids and rocks at accessible depths are associated with recent fault activity. Much of the geothermal resource is available in hydrothermal reservoirs, large pools of hot water trapped in the fissures and pores of underground rock and heated by the surrounding earth. The energy in hydrothermal reservoirs is tapped by converting the heat to electricity.
By using electronics that will function in high temperatures for extended periods, the need for Dewars will be eliminated, dramatically cutting the costs of producing geothermal instrumentation and thereby reducing the cost of geothermal energy.
SOI Technology
Among the electronics Normann and Henfling are testing is an HT83C51 processor with 32 kilobytes of random access memory, produced by Honeywell. Known as silicon-on-insulator (SOI) electronics, they have transistors built on nonconductive silicon, compared to standard silicon chips, which build transistors within semiconductive bulk silicon. The SOI technique cuts current leakage dramatically, allowing the electronics to operate in high-temperature environments.
To fully exploit this technology, Sandia is developing new methods of assembly and supporting hardware. Testing the microprocessor circuit required hard wiring integrated circuits onto a ceramic board using laser-welded connections. This was required because standard printed wiring boards simply don’t exist for use at these temperatures, and common solders melt between 180 and 250 degrees C.
Because testing the individual electronics components in an actual geothermal well is impractical, the Sandia researchers conduct their experiments in a high-temperature oven in one of the Geothermal Research Department’s labs. Instruments on the outside of the oven are connected by ceramic insulated wires to the electronics devices being tested. Each device is tested for function and performance at various temperatures.
Hot Temperature Runs
The longest temperature run of the Sandia microprocessor circuit at 300 degrees C has been 72 hours. The test was interrupted only to cool the oven to add new experiments. The same electronic devices have logged 2,500 hours at 250 degrees C over a period of months.
Normann anticipates that the use of high-temperature electronics could cut the cost of geothermal logging tools by $4,500 each, or 20 percent of the total tool cost, by eliminating the Dewar. To make the logger practical, however, additional testing and system development must be done. For example, Ronald Guidotti is working to develop a suitable high-temperature battery that could function in the geothermal environment without need for thermal isolation.
“Based on the progress being made at Sandia toward the development of high-temperature electronics instruments that can operate continuously at 300 degrees C, the successful development of a Dewarless data logger in the near future is a real possibility,” Normann says.
Technical Contact:
Randy Normann, ranorma@sandia.gov, (505) 845-9675