ALBUQUERQUE, N.M. — Normally, bare metal sliding against bare metal is not a good thing. Friction will destroy pistons in an engine, for example, without lubrication.
Sometimes, however, functions require metal on metal contact, such as in headphone jacks or electrical systems in wind turbines. Still, friction causes wear and wear destroys performance, and it’s been difficult to predict when that will happen.
Until now.
Sandia National Laboratories materials scientists Nicolas Argibay and Michael Chandross and colleagues developed a model to predict the limits of friction behavior of metals based on materials properties — how hard you can push on materials or how much current you can put through them before they stop working properly. They’ve presented their results at invited talks, most recently the 2016 Gordon Research Conference on Tribology, and in peer-reviewed papers, including a recent Journal of Materials Science article.
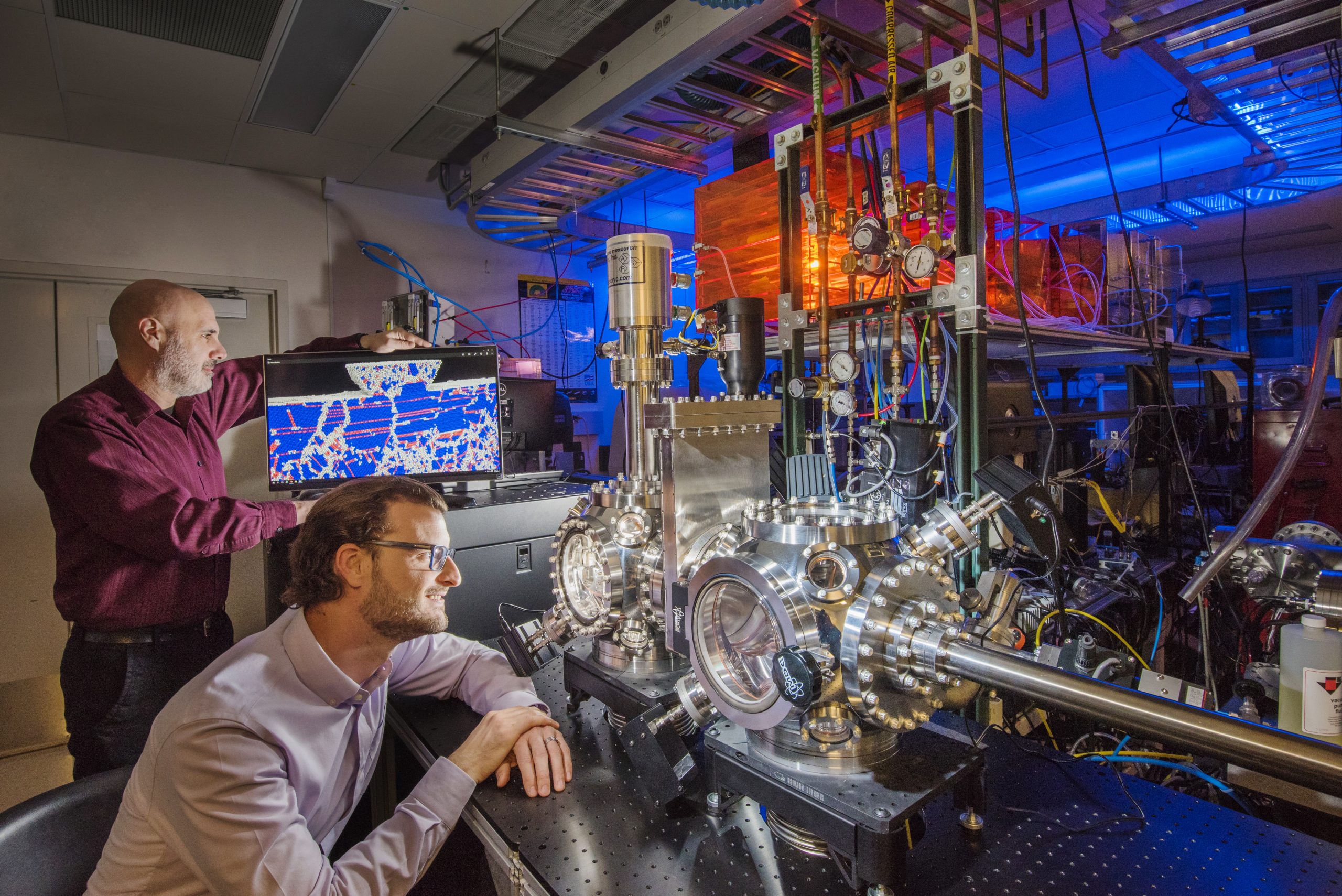
Their model could change the world of electrical contacts, affecting industries from electric vehicles to wind turbines. Understanding the fundamental causes of failure in metal contacts allows engineers to step in and fix the problem, and potentially lights up more paths toward new materials designs.
Linking science to engineering applications
“It’s a tool to do design and it’s a tool to do science,” Argibay said. “It’s really that link between fundamental science and engineering applications.”
The discovery of how to predict the friction behavior of metals began as a study of specific materials for projects.
“It’s a moment where you go from just having to say, ‘The materials behavior will be this because we measured it in those conditions’ to saying, ‘I can tell you what conditions you can run in and get the behavior you want,’” Argibay said. “In fact, we provide guidelines for developing new materials.”
Designers choose materials based on engineering rules of thumb under certain operating conditions, using the conventional wisdom that harder materials create less friction.
But Sandia’s research demonstrates the stability of the microstructure governs the friction behavior engineers care about, and that changes how engineers can think about design when they characterize and select materials, the researchers said.
The team studied pure metals, such as gold and copper, to break down the friction problem by looking at the simplest systems. Once they understood the fundamental behavior of pure metals, it was easier to demonstrate that these ideas apply to more complex structures and more complex materials, they said.
Idea began with separate project
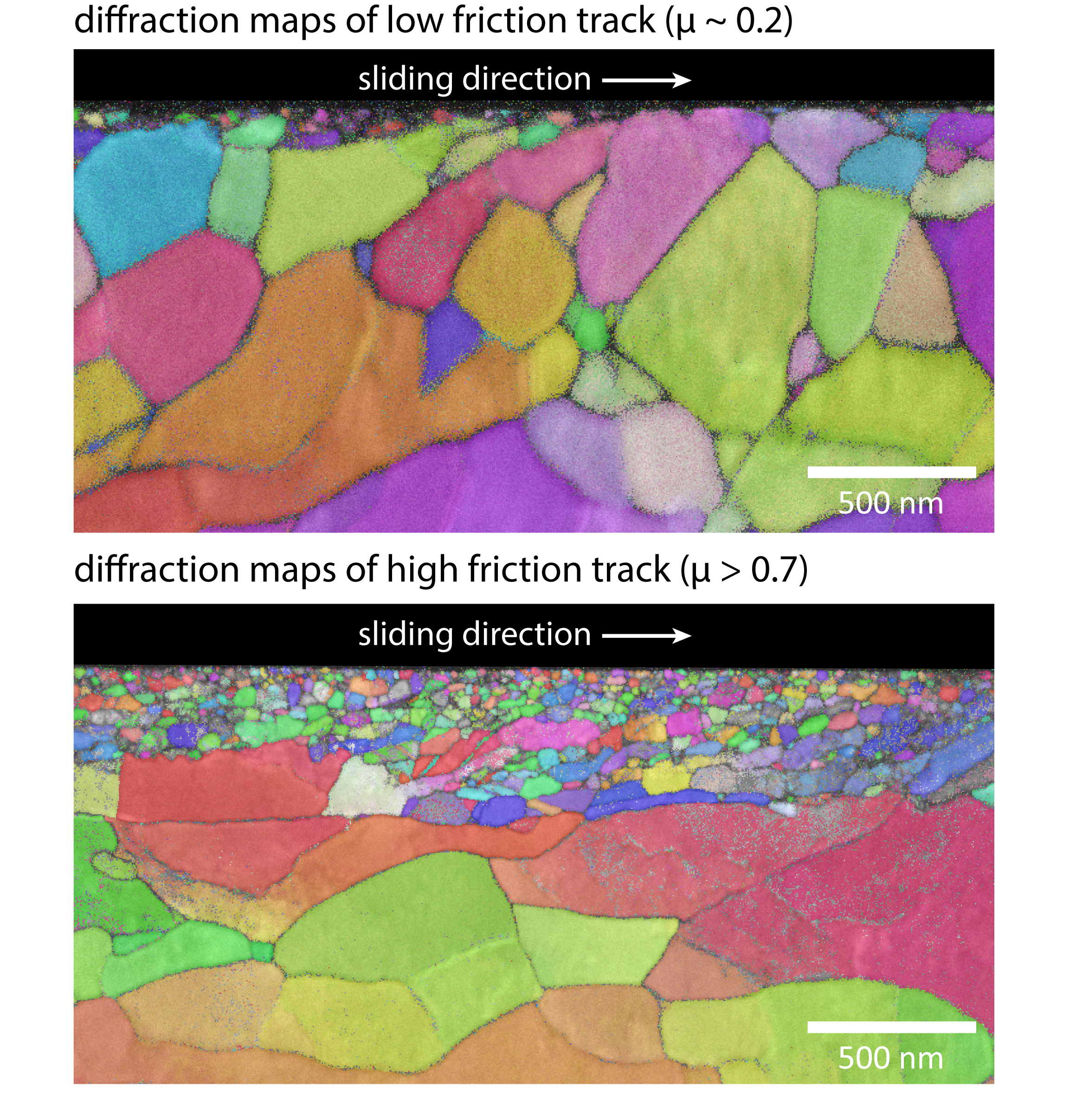
The idea developed in a convoluted fashion, starting several years ago when Chandross was asked for simulations to help improve hard gold coatings — soft gold with a minor amount of another metal to make it harder. Gold is an efficient, corrosion-resistant conductor, but generally has high adhesion and friction — and thus high wear.
That project produced a paper that excited Argibay, who told Chandross he could do experiments to prove the concepts the paper described.
“From those experiments, the whole thing exploded,” Chandross said.
“We looked at the pure metals as a way to validate some of the hypotheses we had from Mike’s analysis of more complex systems,” Argibay explained. “If these ideas work in more complex systems, they ought to work in the most difficult scenario, the least likely scenario conventionally, and they did.”
Sandia’s work has implications for the growing worlds of wind turbines and electric vehicles, where companies seek an edge over the competition. The demand for electric cars and alternative ways of making electricity are likely to expand and in turn create demand for new technologies.
Argibay is helping design and develop a prototype rotary electrical contact for wind turbines that began as a Laboratory Directed Research and Development (LDRD) project.
“Basically we’re bringing back technologies that were discarded because they didn’t really understand the materials and couldn’t make them work where and how they wanted to,” he said.
New projects are ongoing
The project is exploring copper against a copper alloy for a high-performance, efficient electrical contact. That could allow the wind turbine industry to explore designs that weren’t possible before.
In addition, the electrical contacts industry, which now uses alternating current in devices, might finally be able to turn to direct current devices as higher performance alternatives. As a possible interim step, Sandia researchers are exploring metallic electrical contacts as a drop-in for some applications, avoiding major changes in how the devices work.
If they demonstrate the theory is sound, then engineers can change how they think about the fundamentals of design in some of these devices, they said.
Follow-up funding allowed the team to study the variable of temperature, and now Chandross has begun an LDRD project to look at metals with other structures. Previous work has been done with face-centered cubic structured metals. Chandross’ project seeks to understand friction in body-centered cubic metals, BCC metals, most commonly used for structural purposes. Researchers are looking at iron and tantalum.
Conventional wisdom holds that BCC metals won’t produce low friction. “This is one of those instances where understanding the molecular scale or atomic scale mechanisms caused us to say, ‘Yes, but they’re bad only if you’re not in the right conditions.’ What happens when you are in the right conditions?” Chandross said.
BCC metals could open up more design and engineering possibilities for wind power generation and electric vehicles, improving efficiency and ultimately reducing maintenance and manufacturing costs.