ALBUQUERQUE, N.M. — Researchers at the Department of Energy’s Sandia National Laboratories have designed a wireless, battery-free sensor that would power itself by converting mechanical energy from the subtle vibrations of buildings and bridges into electrical power.
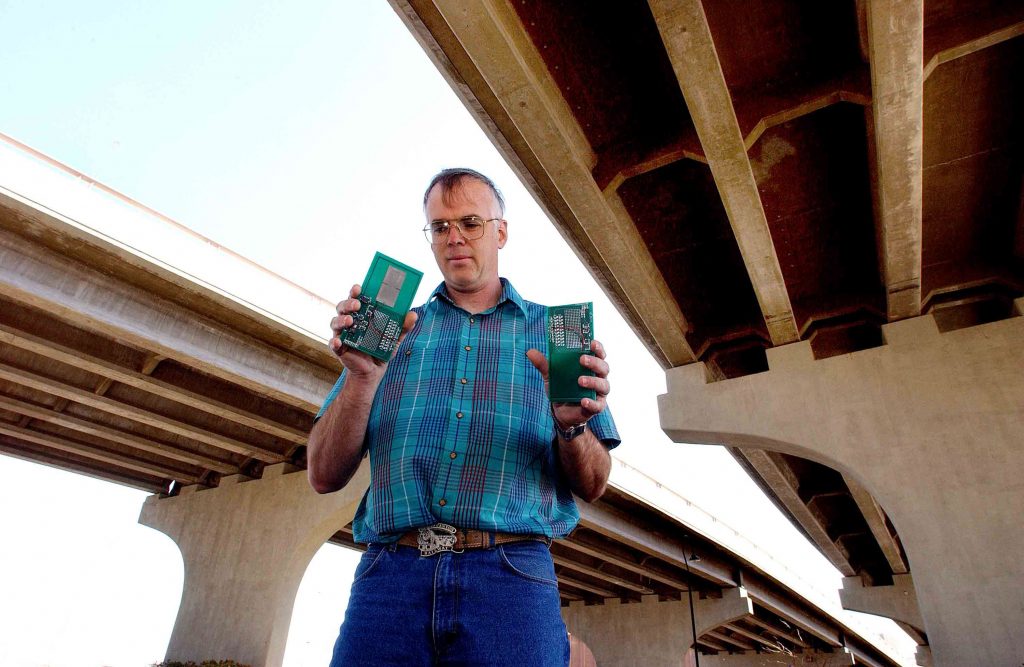
It could use this vibration power to take measurements, then store the data in a memory device that can be read from outside the structure — through concrete, steel, and other building materials — with a commercial radiofrequency (RF) tag reader used by trucking and warehousing operations to track tagged inventories.
Civil engineers might use such a device to check the health of a structure — a hospital, government building, dam, or tunnel — following an earthquake, storm, bomb blast, or other catastrophe, says Kent Pfeifer, who conceived the device and demonstrated its feasibility along with Sandia colleagues Sarah Leming, Art Rumpf, and Robert Waldschmidt.
Because the sensor system requires no hookups to batteries or wires, it could be embedded into a structure during construction and forgotten until a need arises to take a reading.
“If you bend a beam or buttress to a certain point, the next time you bend it, it is going to break,” says Pfeifer. “This technique might lead to self-powered sensor packs that can take a variety of measurements over a long period of time and store them until needed.”
Creation of the device is supported by Sandia’s Architectural SuretySM program, which seeks to improve the safety, security, and reliability of engineered structures through technologies and scientifically validated policy changes. (See https://newsreleases.sandia.gov/bracing-ourselves-against-terrorism-and-catastrophes/.)
No batteries, no wires
The system’s power plant is a swath of piezoelectric material attached to a structural element, such as a beam. (A piezoelectric material produces electricity when subjected to strain. The strain changes the electromagnetic alignments of vibrating crystals in the material — the same natural vibrations that keep time in a quartz crystal watch — to produce a net electrical charge.)
Each time the beam bends from a load on the structure (for instance, when a tall building sways in the wind or a truck traverses a bridge), the piezoelectric ceramic generates a tiny parcel of charge — about 100 microcoulombs is all — which is stored temporarily in the system’s capacitance bank. (It would take almost 1 million microcoulombs to operate a household light bulb for one second.)
This stored charge is sufficient to power the low-power microsensor system for a fraction of a second, long enough to take a simple reading.
If strains on the piezoelectric exceed a predetermined threshold — as the result of a significant tremor in the structure, for instance — the microprocessor could turn on, command the sensor to take a measurement, commit the reading to the RF tag’s flash memory, and quickly shut down into its power-conserving sleep mode.
To retrieve the stored data, a structural engineer might point a commercial hand-held tag reader at the structure near the embedded microsensor system. The embedded tag’s resonant circuit harvests RF energy from the hand-held reader through changes in the circuit’s impedance, making it possible for the hand reader to power the tag’s response remotely.
Uses not yet explored
So far the Sandia team has demonstrated a system that powers a microprocessor generated from vibration only and illustrated an approach to storing and retrieving sensor data taken by such a system, says Pfeifer.
“There’s still more to be done,” he says, including integrating and testing a complete self-powered microsensor system. “But we’ve shown that this is a viable approach to monitoring structural health.”
“A finished device could provide thermal measurements, stress measurements, deflection and strain measurements, or other information that could be stored over time in a database or captured immediately after an event to help plan an evacuation of a high-rise building, for instance,” says Rudy Matalucci, Architectural SuretySM program manager.
Wireless microsystems might initially be employed in structures to predict fatigue or failure of key structural elements, keep track of the number of stress cycles a bridge endures as heavy trucks cross it, or determine the integrity of key structures such as hospitals or emergency command centers following an insult.
The technique might also be used in any application where a self-contained, no-maintenance monitoring capability is needed over a long period of time, says Pfeifer.
Stacks of piezoelectric generators might make higher-power applications possible, perhaps continuously powering embedded clocks.
“I’m sure we haven’t thought of all the possible applications,” adds Pfeifer. “This has never been done before.”