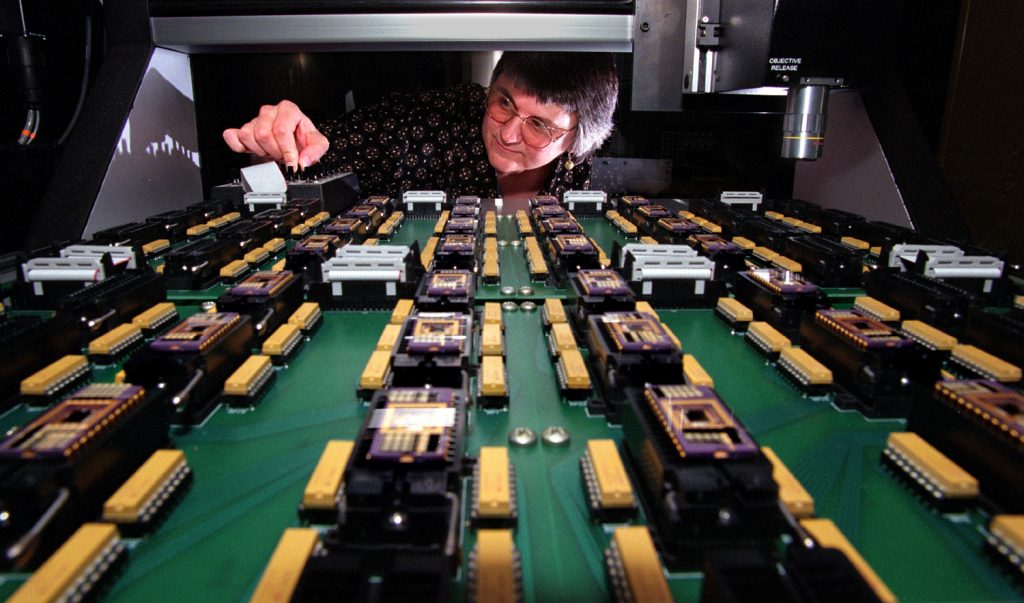
(Photo by Randy Montoya)
Download 150dpi JPEG image, ‘MEMtest.jpg’, 1.1MB
ALBUQUERQUE, NM — Work being done at the Department of Energy’s Sandia National Laboratories to determine the reliability of Microelectromechanical systems (MEMS) may mean that one day soon most electronics devices will contain the micron-size machines.
MEMS, minute machines imperceptible to the human eye with moving parts no bigger than a grain of pollen, are already found in many devices, from computer game joy sticks to car airbag sensors and from inkjet printers to projection displays. But their use may expand and change the electronics industry if they are proven to be highly reliable.
Instrumentation designed by Sandia’s Reliability Physics Department, and a physics-based predictive model developed by Bill Miller, the department’s manager, are being used to test micromachine reliability.
“We constantly ask the questions — how reliable are they and can we use them in real applications?” Miller says.
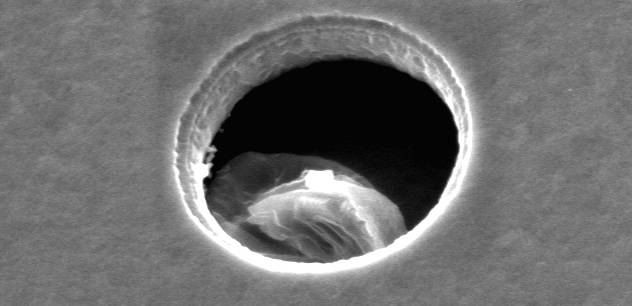
The use of MEMS in electronics devices is on the increase, and some industry experts believe that the market for them will grow to more than $30 billion worldwide by early next century. That is quite a change from 1989 when they were laboratory curiosities with low power, short life times, and few practical proposed uses.
Miller calls MEMS the “future of electronics.”
“I liken it to the integrated circuit industry at the end of the 1960s — a lot of potential, but no one really knew how big it could get then,” he says.
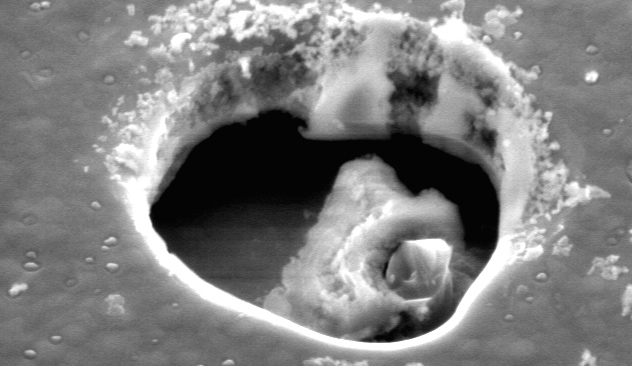
Sandia has become a recognized leader in this emerging field, developing unique technologies that lead to complex mechanical systems on a chip with their on-chip control electronics. While Sandia’s interest in MEMS stemmed from their potential use in weapons, the spillover to the commercial arena was inevitable.
“It soon became apparent that one of the greatest challenges for the successful commercialization of this new technology is in proving its reliability,” Miller says.
Importance of reliability of MEMS
This is true for four reasons. First, many promising applications of MEMS will be in critical systems where the cost of failure is high. Second, MEMS failure mechanisms are poorly understood. Third, MEMS technology continues to evolve rapidly. And fourth, design tradeoffs must account for reliability, lest warranty costs grow.
When Miller’s department started MEMS reliability testing two years ago, the general belief was that polysilicon, the material from which micromachines are made, is very brittle at these dimensions. Most reliability concerns centered around material fractures.
“What we have done, which is totally new, is ask the question — how do they really fail. No one had any real data,” says Sandia reliability team leader Danelle Tanner.
Previous reliability tests had all been done on small scales, looking at one, two, or three devices at a time. The team studied hundreds simultaneously.
SHiMMeR tests micromachines’ reliability
The first step was to build an instrument in which to test the micromachines. Norm Smith designed and constructed SHiMMeR (Sandia High-volume Micromachine Measurement of Reliability), a Plexiglas enclosure that contains a base for testing as many as 256 MEMS parts at a time and a high-powered optical microscope and video camera to observe and record the failures.
Each MEMS device is attached to cables through which signals are sent to activate the micromachines. Humidity, believed to be a major factor in MEMS failure, can be controlled in SHiMMeR. The researchers use the microscope to observe the micromachines operating.
SHiMMeR is a one-of-a-kind machine. Because no commercial system was available to do this type of work, the Sandians had to hand-build the machine. Scientists from around the world come to Sandia to observe SHiMMeR. By running the micromachines until they break — the current record is seven billion revolutions — and then cutting a cross section through the gears with a focused ion beam and looking at them through the microscope, Miller and his colleagues also obtained a good idea about what makes MEMS fail and when and where failures occur.
What they discovered statistically last September, after nearly 1 1/2 years of testing and compiling data, was quite different from previous expectations that microengines malfunctioned because of polysilicon fractures.
MEMS fail by wear
“We found they fail by wear, much like a car engine fails without oil. The individual parts get so worn that they jam,” Miller says.
Although there are many types of wear that may contribute to MEMS’ failure, Miller focused on adhesive wear, which involves parts rubbing and causing small pieces to rip off. These pieces attract and stick to each other, particularly in high humidity environments, resulting in regions where the micromachines begin to catch and fail.
The researchers learned that the polysilicon at these dimensions was extremely flexible and tough, not at all brittle.
Simultaneous to the stress and failure study, Miller developed a physics-based model that predicts when parts fail. The results derived from the model — an equation taking into account strength, adhesive wear, critical volume, pin joint radius, applied force, resonant frequency, and quality factor — were “remarkably similar” to the actual results from the physical testing.
Miller says the successful predictive model is significant because it now means that MEMS reliability may be tested without waiting the days, weeks, or months that it takes for parts to fail.
“We can now predict wear-out — how long the device will last — for these tiny machines through accelerated testing and the model,” Miller says. “This makes MEMS more feasible for further development and actual use. The floodgates are about open and MEMS will soon be in many applications, because they will be all the more reliable due in part to our work at the Labs.” More information about MEMS can be found at the Website http://www.mdl.sandia.gov/Micromachine.
Technical contact:
William Miller, millerwm@sandia.gov, (505) 844-7161