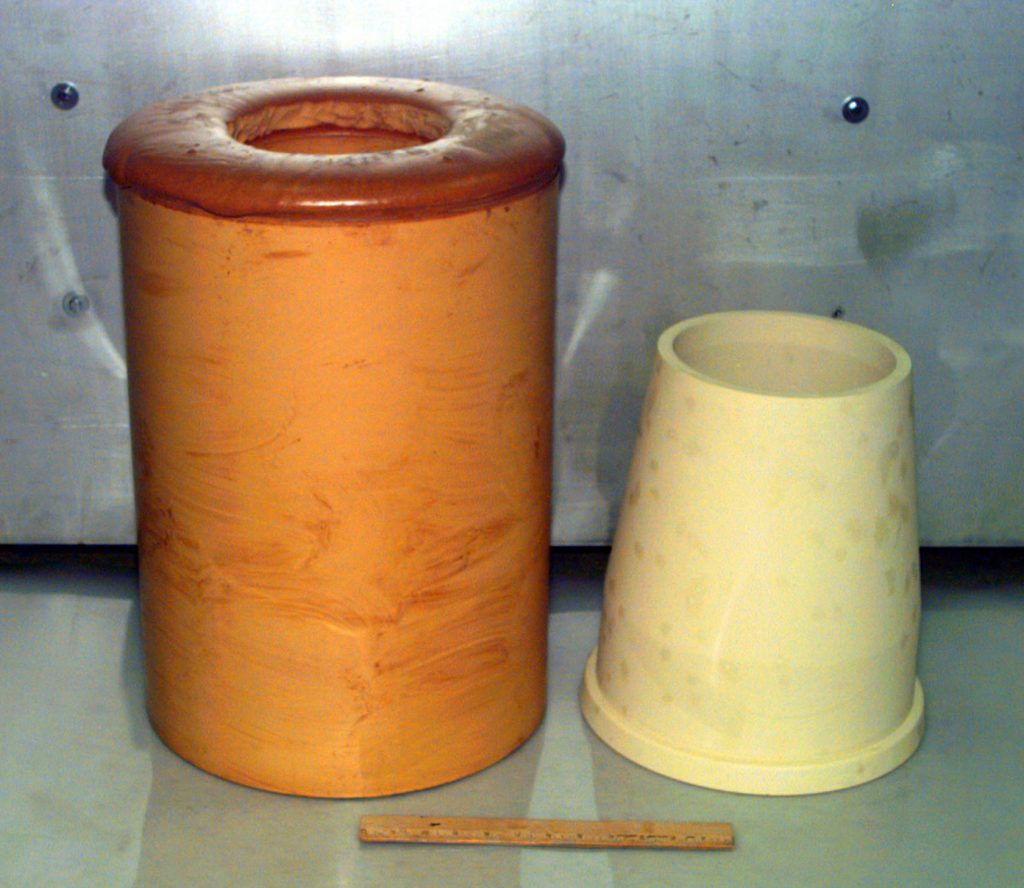
Download 300dpi JPEG image, ‘wpp-foam1.jpg’, 416K (Media are welcome to download/publish this image with related news stories.)
LIVERMORE, Calif. — Researchers at the Department of Energy’s Sandia National Laboratories in Livermore, Calif., have developed a high temperature, high strength structural support foam, TEPIC, that has proven to be an exceptionally versatile material for use as molded-to-shape models as well as prototype and production run tooling for composites manufacturing.
Scott Vaupen, a business development associate at Sandia, said additional applications for the new material may include prototype-injection-molding tooling, hot-embossing tooling, high temperature adhesives, and structural uses as core materials. Preliminary market research, said Vaupen, suggests that TEPIC can have a significant impact on the $100 million global composite tool manufacturing market.
Because it can be poured into a mold or machined from cast billets (much like conventional tooling board stock), TEPIC offers significant advantages over tooling board materials in current use. These materials are available only as thin-slab stock, so larger applications require that multiple boards be bonded together. These laminated structures can separate, even after one use cycle, and their repair becomes cost prohibitive over multiple processing runs.
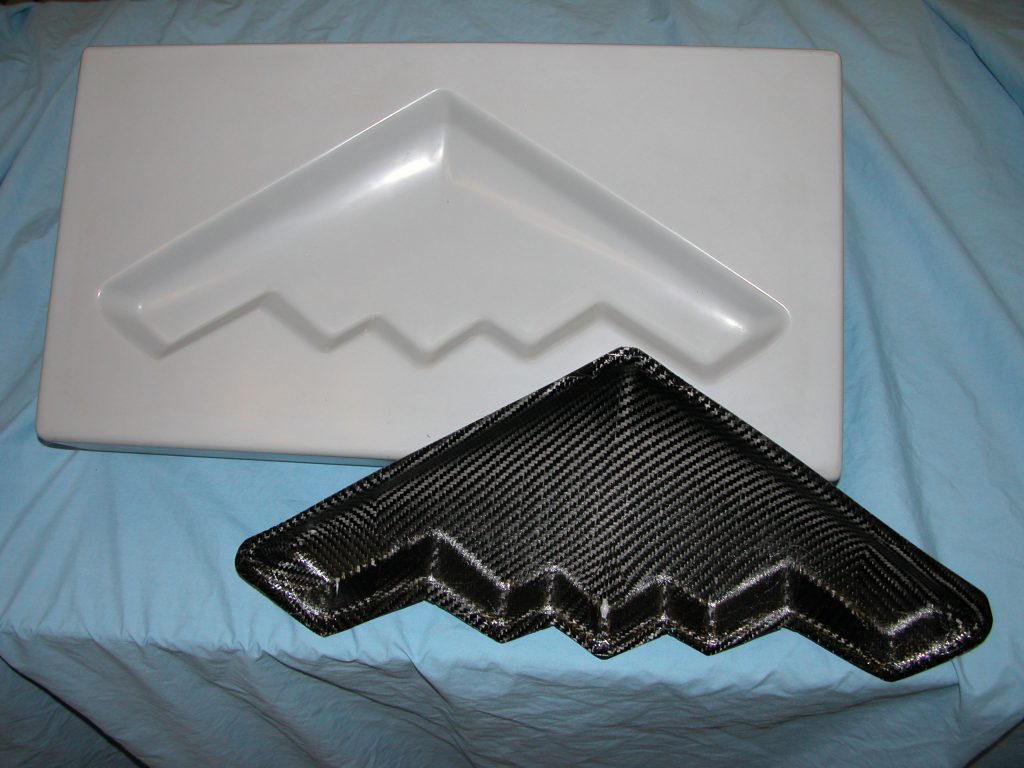
Download 300dpi JPEG image, ‘wing-mold.jpg’, 612K (Media are welcome to download/publish this image with related news stories.)
In comparison, TEPIC can be fabricated in much greater section thicknesses than other conventional slab stock materials, eliminating the need to bond and repair large tools. TEPIC is dimensionally stable and retains strength to temperatures in autoclave processing in excess of 400°F at 100 PSI. In contrast, other lightweight polymer-based tooling materials have limited utility due to their maximum-use temperature of less than 310°F. While TEPIC is expected to be cost competitive with existing tooling boards, it can be used to process higher temperatures curing composites (>350°F). In addition, TEPIC can be used with many standard mold releases and gel coats for multiple part removal and surface finish requirements. It is also repairable using a commercial adhesive system.
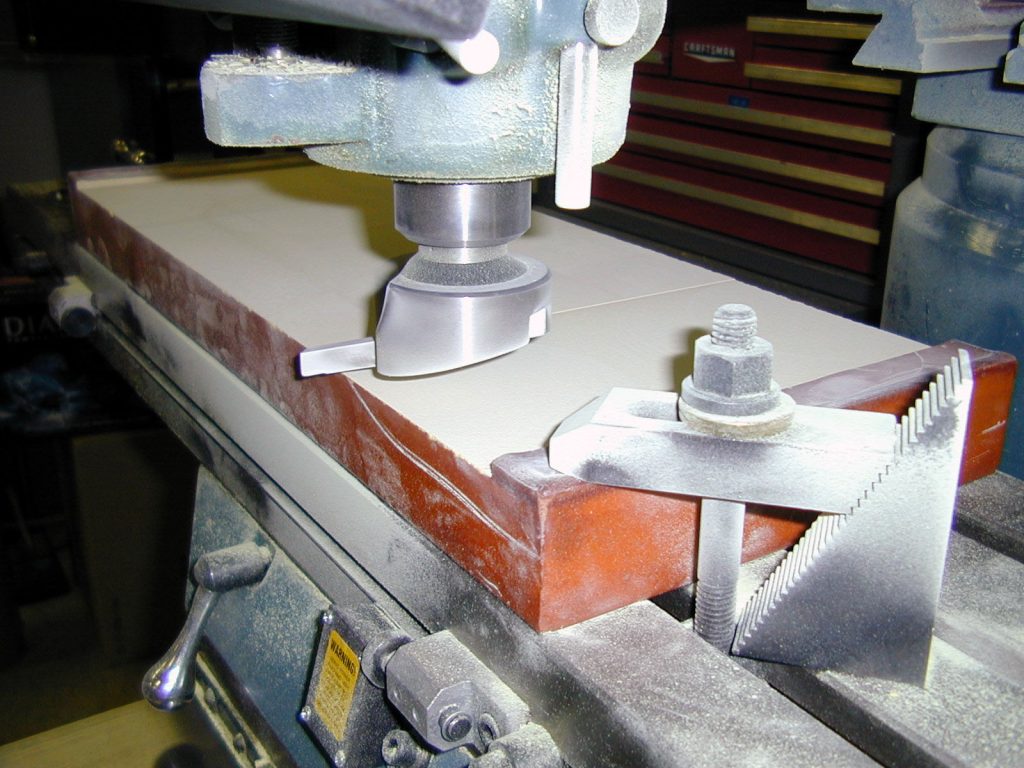
Download 300dpi JPEG image, ‘machining-tepic5.jpg’, 412K (Media are welcome to download/publish this image with related news stories.)
TEPIC compares favorably against metallic composite tooling as well. Tooling fabricated from metals and alloys are expensive, difficult to repair, heavy, and unwieldy in larger dimensions. TEPIC is about five to ten times more affordable than bulk aluminum and four times lower in density. Weight and cost savings are even greater in comparison to more specialized alloys such as Invar 36.
For information regarding possible collaboration towards commercialization or licensing opportunities, contact Scott Vaupen at (925) 294-2322, sbvaupe@sandia.gov.