ALBUQUERQUE, N.M. — Imagine untwisting a finger-size spring, then holding the flame from a lighter underneath the unraveled section. Like magic, it twirls itself into a spring again because the metal alloy remembered its original shape.
Sandia National Laboratories researchers think such shape-memory alloys could be used to improve safety in weapons components in a fire or other accident. Materials scientist Don Susan said a thermal device made from a high-temperature shape-memory alloy might, for example, close or open a switch or lock a gear to prevent it from turning.
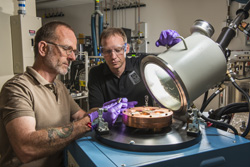
“It’s almost unlimited what you can think of, what you can do with shape-changing alloys,” he said.
Susan is principal investigator for a project that aims to create high-temperature shape-memory alloys for weapons components. Accomplishments so far:
- Researchers made new alloy compositions, including nickel titanium platinum, nickel titanium palladium and nickel titanium hafnium, and filed technical advances for those compositions. Filing a technical advance is a first step in documenting an invention for a later patent application.
- The team has characterized such key properties of the materials as the way they change shape, strength and ductility.
- Team members have produced prototype parts that show shape change at desired temperatures.
- Sandia is the first to demonstrate a property called super-elasticity in higher temperature shape-changing alloys, and filed a technical advance for that. Super-elasticity is a rubbery sort of behavior in metals, such as eyeglass frames that twist without snapping. Susan said Sandia doesn’t currently intend to exploit this property but it could provide future design options.
The project, now in its third and final year, is funded by Sandia’s Laboratory Directed Research and Development program.
Alloys remember original shape
Shape-memory alloys work somewhat like the thermal sensor in a building’s fire sprinkler system. That thermal sensor is made of a liquid that expands and breaks a glass enclosure, triggering a switch that turns on the sprinklers. Similarly, shape-memory alloys change shape instead of simply expanding.
“If you bend a wire, it’ll go back to straight if it was originally straight,” Susan said. “If it was originally bent and you made it straight, it will go back to bent. It will remember a shape when you heat it up.”
Such an alloy can trigger a process simply because it’s able to change shape, said project manager Jim McElhanon, who started the project with weapon safety engineer John Debassige. Susan later replaced McElhanon as principal investigator. Other team members are Tom Buchheit, Jordan Massad, Don Bradley, Mark Reece and Tom Crenshaw.
“I truly believe this research on [high-temperature] shape-changing alloys will allow us to create new devices that significantly impact nuclear weapon safety. The shape-memory alloys we are developing can passively change shape via exposure to a particular temperature or actively change shape by passing current, which generates heat, through the material,” McElhanon said.
Shape-memory alloys have been around for decades and various types are sold commercially. They’re commonly used in such medical appliances as stents that change shape at body temperature. A tiny stent, stored at below-body temperature, can be squeezed small enough to fit into an artery, then opens up the artery when warmed to body temperature, Susan said.
Shape change needed at specific temperatures
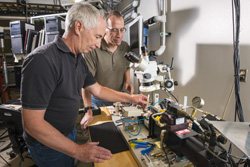
The Sandia alloys can change shape at temperatures below room temperature to greater than 500 degrees Celsius, or about 930 degrees Fahrenheit.
Commercial alloys change shape at temperatures that don’t meet Sandia’s needs, Susan and McElhanon said. Sandia built upon recent research into higher temperature shape-memory alloys to create its own alloys.
“Folks at Sandia were studying these alloys decades ago, but the temperatures were always too low to be useful for our parts until these new alloys came along over the past 15 years or so,” Susan said.
Any shape change has to take place above the temperature at which components are manufactured, Susan said.
“You don’t want this to happen when you’re making the parts,” he said. “You don’t want it to happen when it’s sitting out in the sun either. It has to be higher than that.”
In April, the Consortium for the Advancement of Shape Memory Alloy Research and Technology (CASMART) voted to add Sandia as a member. Government, academic and industry experts started CASMART in 2006 to share applied research on shape-memory alloys.
“Joining the consortium is a huge step forward for the labs,” McElhanon said. “We are collaborating with the world experts in the area.”
Computer models to show behavior
Sandia works on shape-memory alloys with Ron Noebe and his colleagues at NASA’s Glenn Research Center in Ohio and with colleagues at Texas A&M University in College Station. NASA and Texas A&M are both consortium members. NASA is interested in the alloys for flight applications, while the university works on materials processing — turning the alloys into specific shapes, Susan said. Texas A&M researcher Brian Lester worked with Sandia this summer on computer models of shape-memory alloy behavior.
“Our computer models can’t handle something that changes shape like that,” Susan said. “When you heat something up, it expands a little bit and when you cool it down it contracts. We can handle that in the computer codes, but not this more dramatic shape change.”
Susan envisions future Sandia research on shape-memory alloys for wind and solar energy and perhaps satellites.
“They are really interesting materials,” he said. “Most of what we work on at Sandia is stainless steel, aluminum, the kinds of things we’ve worked on forever and that most of our parts are made of. So it’s interesting to work on something different and explore the possibilities.”