Microscope tip charts relaxation of solid liquid
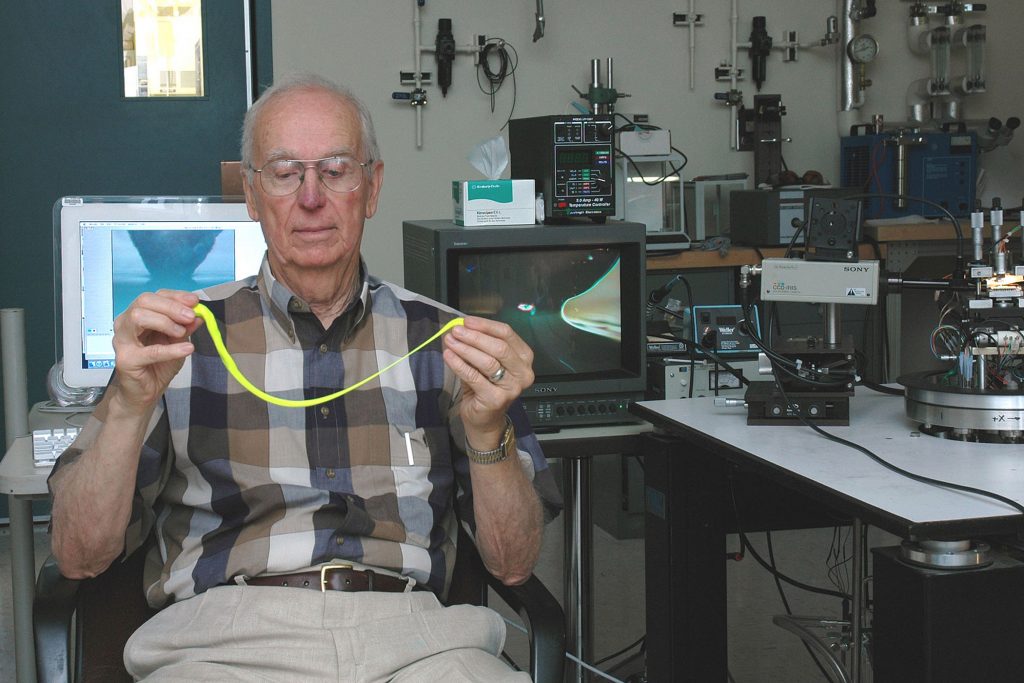
Download 300dpi JPEG image, “jack-houston.jpg,” 412K (Media are welcome to download/publish this image with related news stories.)
ALBUQUERQUE, N.M. — Squaring off with Silly Putty® — a material scientist’s worst nightmare — a Sandia National Laboratories researcher has demonstrated that a unique microscope quick enough to measure changes in this “liquid solid” may be the most effective tool for measuring less extreme plastic behavior in the structures of more widely used materials.
Playing off the old saw about New York, Sandia researcher Jack Houston says about the continuously puddling child’s toy, “If I can measure the plastic behavior there, I can do it anywhere.”
Materials made of matrices holding embedded particles are increasingly common in modern life. Their realms include (in addition to Silly Putty) such widely varying products as golf club shanks, solid rocket fuel, polymers mixed into cement to help bond rebar, rubber bands, and many other modern implements.
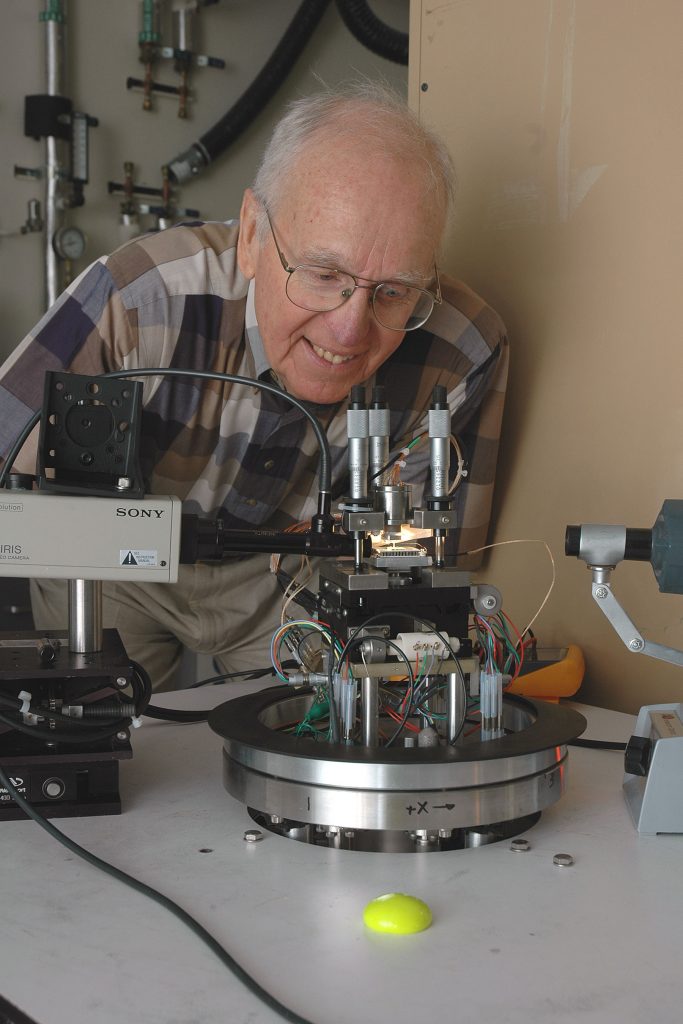
Download 300dpi JPEG image, “sillyputty.jpg,” 412K (Media are welcome to download/publish this image with related news stories.)
When the matrices of these materials age over time, golf clubs become creaky, rocket fuel blows up like a bomb, cement weakens, and rubber bands snap when even slightly stretched.
Of all these materials, Silly Putty possesses one of the broadest ranges of plastic behavior. Leave a ball of it for a few minutes on a table and it flattens to a thin disk. More technically put, the polymeric stuff creeps forever under a static load. Knead it into a ball and it bounces like rubber. Worse, the stuff strongly adheres to probes: Blind sensors register little data. Adhesion coupled with creep causes the conditions of any experiment to continually change.
A tool that could measure the plastic behavior of Silly Putty — the material world’s champion shape changer — could characterize matrix deterioration of almost any similar substance to alert manufacturers or users before the material fails. Timetables of matrix decay could be established, based on the pace at which a particular matrix changes. And measurements made at the level of individual particles, rather than bulk measurements of the entire structure as currently done, offer possibilities of intelligently varying the mix of materials to produce better consumer products , rather than through expensive, lengthy gross trial-and-error.
In a paper accepted for publication in the Journal of Polymer Science B (Physics), in work supported by DOE’s Office of Basic Energy Sciences, Houston reports that the Interfacial Force Microscope (IFM) was able to achieve such consistent measurements before the Silly Putty could shift enough to invalidate the data achieved by the scope.
The IFM is unique in being able to obtain quantitative data of a material’s time-dependent mechanical properties. It’s like the atomic force microscope, or AFM, but that popular technique suffers from being mechanically unstable, says Jack. It snaps in and out of contact, like two kitchen magnets brought together controllably, one in each hand. “It can’t be done!” Houston says.
The IFM, on the other hand, has a tip located on one end of a very small “teeter totter,” which is supported by torsion bars above two tiny capacitor pads. When a sample is brought very near the tip, the force of attraction between the tip and sample causes the teeter totter to rotate slightly. This change increases the capacitance of one pad and decreases that of the other. A feedback system places the proper voltages on the capacitor pads to drive the rotation back to zero. Forces can be measured quantitatively by the amount of voltage necessary to achieve that balance.
A probe deforms a target when it pushes on it. In return, the force against the probe tip changes with time and depends on the nature of the material. Suddenly advancing the tip into Silly Putty causes a springy deformation and a correspondingly large initial force, which rapidly decays as the material creeps away in a viscous flow. This response is measured by the voltage induced on the capacitor pads that keep the tip stable.
“Such results tell us how much stress the material can tolerate and over what period of time the stress can be maintained,” says Houston. “That can be translated into the material’s frequency response.” The microscope measures this stress response in a few seconds, with results that matched 10 to 12 individual frequency tests by a classical rheometer.
Rheometer tests are done on bulk samples and consist of a series of measurements over a range of frequencies. Such measurements can take several minutes, during which time the sample can creep and change the experimental conditions.
There are currently 17 IFM machines in use at Sandia and various universities around the US and in Canada.
Houston expects more next year when a newly patented laser interferometric measuring system replaces the simple radio-frequency bridge system that can’t be scaled to smaller sensor dimensions. The new system achieves greater sensitivity.