Optical innovator uses soda-straw-like tubes to solve widespread sensing problems
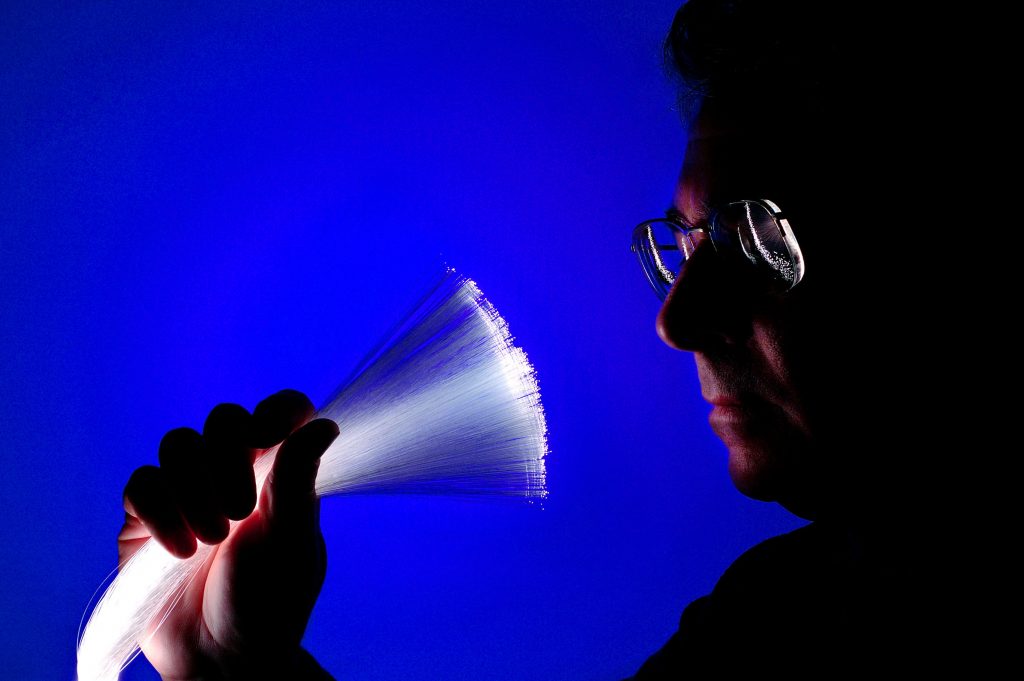
Download 300dpi JPEG image, ‘light-simple.jpg”, 644K (Media are welcome to download/publish this image with related news stories.)
ALBUQUERQUE, N.M. — There you are, tapping your fingers on the cold steering wheel as your windows cloud over from your breath. How could you have known your car battery was that low?
Sending weak beams of light through inexpensive glass tubes that resemble soda straws, Sandia National Laboratories researcher Jonathan Weiss — dubbed by some the “light wizard” — can inexpensively solve problems ranging from the migration of waste through a landfill to detecting when an automobile battery soon will be too weak to start a car.
Similar sensors also could tell oil field operators when to stop pumping oil from their tanks before the pumps pick up water that accompanies oil from the ground.
The oil/water interface sensor is the subject of a pending Sandia patent application and a research agreement with Custom Electronics, an electronics company in upstate New York. The company is partnering with Sandia, a National Nuclear Security Administration (NNSA) lab, to develop a prototype device from the current bench-top demonstration.
The car battery solution awaits a visionary entrepreneur to put this cheap, safe, patented solution in the hands of the public. And in an invited talk at a recent American Soil Society meeting on Nov. 3 in Seattle, Weiss presented his patented device for detecting hazardous waste movement.
Avoiding the unexpectedly dead battery problem
A turkey-baster-like device inserted into a popped-open port has been the traditional way for a driver to test the amount of acid in a car battery (and possibly splash sulfuric acid on his or her fingertips). Weiss’s simple invention requires no direct human intervention under the hood.
His procedure: factory-inject sulfuric acid or even, possibly, sugared water into a clear glass tube smaller than a soda straw and immerse the tube in the battery”s acid. Glass is inert in acid and should have ample longevity, he says.
Next, send light through the tube and measure the amount that returns. (The light is generated by hardy, inexpensive diodes [LEDs] already mass-produced for traffic signals, house night lights, bike tail lights, and instrument control panels.)
The amount of light that stays in the tube depends on the refractive index of the surrounding solution. If the refractive indices are identical, light would just as soon escape from the sides of the tube as stay within it. That is the case when the tube is filled with sulfuric acid at maximum charge. The refractive index is at first the same as that of the battery acid surrounding it (1.38). But over time, the battery”s acid weakens and becomes more like water (1.33). Its lessening refractive index attracts less light from the tube. The exchange rate, in a manner of speaking, is worsening, and light remaining in the tube (as reflected by a tiny piece of metal placed at the tube”s far end) increases.
A simple solid-state light detector — a photodiode — at the tube”s near end registers more light, therefore, as the battery deteriorates. The detector could easily be wired to activate a dashboard alarm light similar to ones that notify a driver that a seat belt is unclasped.
Sugar water inserted in glass tubing also works well, Weiss says, because the refractive index of water can be adjusted upward by dissolving sugar in it. “Quite a substantial change can be produced, far exceeding that needed for this application,” he says.
While the glass of the tubing does have an effect on light leakage, says Weiss, “the liquid core and liquid cladding are dominant.” The tube is a millimeter in diameter, two to three inches long, and inexpensive: 200 tubes set Weiss back $10 for his experiments. Mass production would drive costs down even lower.
Measuring battery deterioration will become increasingly important as more hybrid electric/gas vehicles, with their high reliance on batteries, take to the highways, he says. Another possible use for the device is for cheap, continual monitoring of battery banks maintained by local phone companies. The batteries are used for back-up power to keep home phones working when wall-current electricity fails due to an outage.
Using light to find the level of oil and water in a tank
Imagine you”re in the oil business and you”ve pumped oil and water (just the way it increasingly comes out of the ground) into a holding tank. You want to retrieve only the oil floating atop the water so you can transport the least possible weight from the oil field to a refinery. How do you know — accurately, safely, and simply — when to stop pumping?
This widespread problem is often solved currently by the most primitive means: An employee opens a hatch and drops a stick into the liquid, possibly inhaling its fumes as pumping is in progress.
With trivial hook-ups and a bit of engineering logic, Weiss shows — at least in laboratory demonstrations — that the answer to this problem can be quickly determined.
Weiss’s recipe: Take two five-foot-long optical fibers made of plastic. Mount them vertically in a tank that holds water with oil on top. Send light down one fiber, and then detect light carried back up by the second fiber. The strength of the detector”s signal depends on the height of the oil/water interface. If the tank is all water, the signal is very strong, and the pumping machine is instructed to stop pumping fluid; there is no oil left.
“The device is immune to electromagnetic interference and will not create sparks in a potentially explosive environment,” says Weiss.
The possibility of sludge building up on the device, muting the light, as the large tanks are filled and depleted is a potential reliability problem that might be overcome by “potting” the fibers in a clear plastic that repels hydrocarbons, says Weiss.
The transfer of this technology to a private company is the maiden effort of Sandia”s new Mission Centric Venturing program, intended to expedite interactions with industry. The program offers Sandia researchers the alternative of marketing their ideas commercially while remaining at Sandia.
Detection device for landfill
When people are interested in the behavior of a landfill that holds chemicals that may undesirably leach into groundwater, the problem naturally comes up: How can an observer tell what the chemicals in a landfill are doing?
For leaching to occur, liquid must be present.
Weiss’s solution: Arrange two fiber optic cables like snakes, one above the other, in the landfill. Shine a light through the fibers. Because the temperatures of the fibers change the amount of light scattered by them, the emissions can be used to indicate the temperature at any point along the fiber. That temperature is determined in part by how much water is in the surrounding soil. Thus, fluid flowing down through the landfill would produce a clear signal from the wetted, cooled fiber.
Weiss’s innovative fiber optic sensors have received 12 patents in the last ten years — five of them with Sandia and the others with the U.S. Department of Energy.