ALBUQUERQUE, N.M. — Imagine a table with sinuous legs resembling the twisting shape of an inverted swamp cypress trunk. Those flowing legs might make the table stronger, better able to handle whatever someone piles on it.
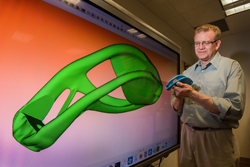
Sandia National Laboratories researchers believe such organically shaped designs, achieved through a technology called topology optimization, could enable better parts for national security systems and other vital uses. Coupled with advanced additive manufacturing, familiar to most people in its 3-D printing incarnation, it opens possibilities for complex shapes that conventional manufacturing methods can’t handle. Partnering the technologies also offers the potential to embed sensors or wiring within a structure as it forms or combine parts to save time and money, reducing the number of joints or other interfaces that could be points of failure.
Before the techniques can be widely employed in high-reliability, high-consequence uses, however, researchers must understand both how to create the best shapes and guarantee material properties.
“There are aspects of this marriage between additive manufacturing and topology optimization that are going to be critical for us to address if we’re really going to do this well,” said Simulation Modeling Sciences manager Ted Blacker. “If all you do is make the same old parts a new way, it’s taking advantage of only a fraction of what is possible in additive manufacturing. And if you make these new optimal parts but you can’t assure material quality, they’re of no use.”
Sandia is well-suited to tackle the problem because of its expertise in computational mechanics and analysis tools it developed in engineering codes such as Sierra and Alegra, modeling tools such as Cubit and expertise with high-performance computers. Sandia also has experience in handling large amounts of data, people who know how to write and adjust codes, skill in materials science and a history of inventing additive manufacturing techniques. In the 1990s, Sandia developed Laser Engineered Net Shaping (LENS), a process to print complex metal parts from powders, and Robocasting, a 3-D process that forces ceramic slurry through a pressurized needle to form a part that is fired in a furnace to harden it. Both processes have been commercialized.
Additive manufacturing handles complex shapes
Additive manufacturing encompasses techniques to make parts or whole assemblies in plastic, ceramic and metal. “We need to develop computational tools that will enable us to make the leap to new types of designs, tools that will make modern computer-aided design systems seem as quaint as drafting tables and T-squares,” said Andre Claudet, a manager in the Precision Mechanical Systems department.
Sandia is particularly interested in an advanced metal additive process that uses a laser to melt successive layers of metal powder to build shapes. It has the potential to make components that perform better and weigh less. However, the process alters a material’s microstructure, which can dramatically affect its properties and how parts perform. Researchers need to understand how the extreme temperatures and heating and cooling rates affect material properties.
The largest barrier for new materials is understanding their properties well enough to certify that they meet rigorous requirements for high-consequence uses. Materials assurance, a key to certification and qualification, is “the first, most immediate obstacle that we need to overcome,” Claudet said.
Important material characteristics, such as strength or ability to withstand stress, depend on many things, including how a material’s internal structure is affected by phase changes — for a simple analogy, think ice melting into water, then refreezing into ice again.
Parts must meet multiple requirements for mechanical, thermal or vibration performance — particularly crucial when something is intended for a nuclear weapon, a satellite or an airplane. “How do you actually verify the material is what you want? For some applications it’s not a big deal. For high-consequence hardware it’s a very big deal,” said Bradley Jared, who works in the Coatings and Additive Manufacturing department.
Techniques together could save material, time, money
Using additive manufacturing with topology optimization could allow several parts to be combined into one, saving material, eliminating possible weak points and removing the need to model what could happen at those interfaces, he said. “Suddenly you’ve simplified a part for simulation, for testing and for qualification,” he said.
Additive manufacturing also is efficient for low-volume production. It’s especially compelling early in product development because frequent design changes can quickly be evaluated, Jared said.
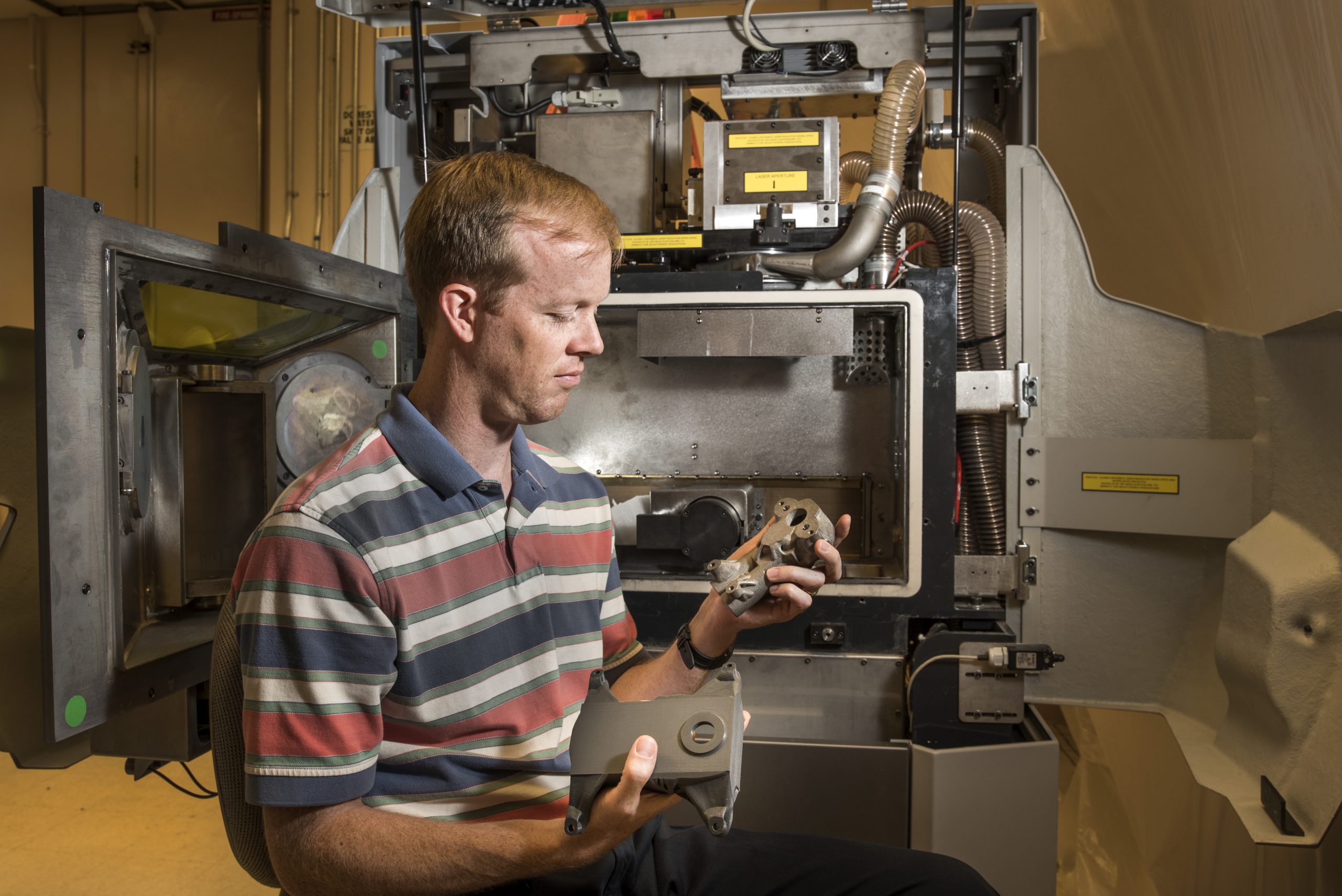
The technique could save time and money in the near term in tooling, fixtures and jigs used to manufacture components, since most tooling items don’t have to be certified like an actual part, said Materials Engineering and Manufacturing Science and Technology senior manager Mark Smith. “We’re already making very extensive use of additive in those areas,” he said.
Certifying materials will perform as expected requires experiments using instruments to understand what’s happening and sophisticated computations to verify that material properties meet specifications. For accurate simulations, researchers must identify what happens as the technique lays down successive layers, but it’s difficult to measure temperatures in bottom layers as other layers form on top.
“We can’t embed anything in those lower layers because that would change the behavior,” said Anthony Geller, manager of the Fluid and Reactive Processes department, which models and simulates fluid and multiphase flows. Simulations, aimed at calculating real-world results using large computers, can predict temperatures in inaccessible layers or study parameters like particle size distribution that would be difficult and costly to examine by experiments alone. Experiments can validate the model.
Engineering analysis to predict optimal shapes takes full advantage of additive manufacturing, but poses an extremely difficult computational problem. Static loads, something sitting on top of a table, are easy to include. Dynamic loads, someone jumping on the table, are not.
Diagnostics could include a thermal camera to learn about the melting process and metallurgy. Some studies have used optical cameras to see how powder disburses in a layer and to study the laydown process.
“Right now we don’t have a whole lot of information coming off the machine and off the process,” Jared said. “We don’t know what we don’t know.”
Microstructure properties perhaps could be tailored
Understanding how material forms might eventually lead to custom-tailored microstructure properties.
“So you can have different material, different microstructures, different properties in different regions that can be incorporated as part of the design process if we can understand it well enough,” Smith said. “That’s sort of the long-term vision: You would not only design the geometry, but actually design the microstructure of the part as you build it.”
Engineers today sometimes overbuild because they’re uncertain about material properties. However, topology optimization assumes certain properties as it follows design specifications. “The optimization says that if we have that tiny curved strut that’s very thin, that’s all the material you really need to carry the load,” Geller said. “But if we have to make it thicker because of our uncertainty, we’re losing that benefit.”
Blacker said Sandia is working on “robust optimization,” letting calculations derive a shape that will meet requirements with point-by-point uncertainties in material properties or in loading conditions. Such uncertainty quantification determines the likelihood of outcomes when some aspects of a problem aren’t known, and predicts results in a statistical sense.
With topology optimization, engineers start with an allowable space — the area where the part fits — then specify functional requirements, “how heavy they will allow it to be, what material they want to use, the loads and the constraints,” Blacker said. “They allow the optimization calculations to determine where the material is needed, placing material only where it will be used most effectively to meet design demands.”
Designs are driven by the functions required
Thus, a designer no longer focuses on creating a shape, but drives the design by the function required, perhaps choosing tradeoffs between such requirements as rigidity and ability to conduct heat. Prioritizing stiffness produces a shell-like structure, with material pushed outward to maximize rigidity. Making thermal transfer more important produces a structure with more massive legs, natural paths for heat. If stiffness and heat transfer are equally important, the result is a truss-like structure that adds stiffness but still has material in the legs.
Designers tell the program, “‘Here are my engineering requirements; you create my geometry for me,’ a major revolution in how we do design,” Blacker said.
Topology optimization requires engineering judgment and thinking through the entire problem. Parameters such as feature size control whether you get a tree trunk or a spider web-like structure holding up a tabletop. That means designers must specify the problem carefully. For example, if you don’t tell the program to secure the legs so the table doesn’t move, it adds cross members along the floor to increase strength, even though that also prevents a chair from sliding under the table. “With topology optimization, you get what you asked for, whether that’s what you wanted or not,” Blacker said.
Thus, the technique requires what he calls interactive steering. If engineers watching a shape form on a computer screen realize they didn’t put in enough information, they can stop the program. “Where we stopped we say, ‘Add this additional constraint,’ and let it continue,” Blacker said. “Even though the calculations are being done in batch mode on very large machines, we can still have an interactive design environment on those machines. We think it’s a very powerful addition.”
Additive manufacturing is a tool, not a panacea, and won’t replace traditional manufacturing for everything, Smith said. “We’re not going to print a complex mechanical assembly with precision moving part anytime in the near future,” he said. “But there may be some applications where it offers unique advantages for us.”
He believes Sandia can make significant progress toward tying materials assurance and topology optimization together in three to five years but said it could take a decade or more to reach that ultimate design optimization goal.
Researchers must balance what can be accomplished now against the work still needed to qualify parts. “I don’t want to minimize the potential benefit but I also don’t want to minimize that there’s still a lot of work to be done,” Geller said.