‘
ALBUQUERQUE, N.M. —Sandia National Laboratories researchers seeking to make hydrogen a less expensive fuel for cars have upgraded a catalyst nearly as cheap as dirt — molybdenum disulfide, “molly” for short — to stand in for platinum, a rare element with the moonlike price of about $900 an ounce.
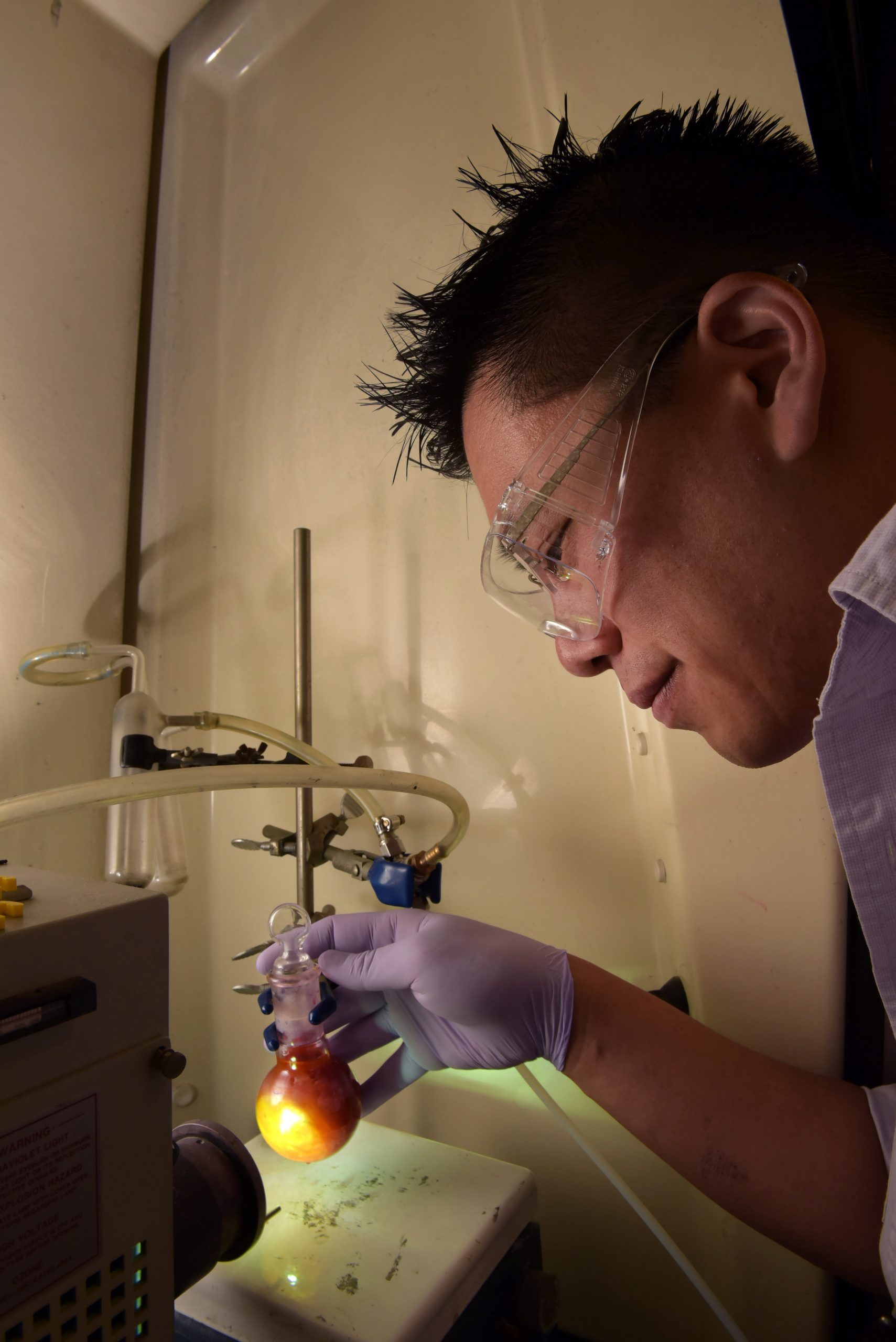
Sandia-induced changes elevate the plentiful, under-$2-per-ounce molly from being a welterweight outsider in the energy-catalyst field — put crudely, a lazy bum that never amounted to much — to a possible contender with the heavyweight champ.
The improved catalyst, expected to be the subject of an Oct. 7 Nature Communications paper, has already released four times the amount of hydrogen ever produced by molly from water. To Sandia postdoctoral fellow and lead author Stan Chou, this is just the beginning: “We should get far more output as we learn to better integrate molly with, for example, fuel-cell systems,” he said.
An additional benefit is that molly’s action can be triggered by sunlight, a feature which eventually may provide users an off-the-grid means of securing hydrogen fuel.
Hydrogen fuel is desirable because, unlike gasoline, it doesn’t release carbon into the atmosphere when burned. The combustion of hydrogen with oxygen produces an exhaust of only water.
In Chou’s measured words, “The idea was to understand the changes in the molecular structure of molybdenum disulfide (MOS₂), so that it can be a better catalyst for hydrogen production: closer to platinum in efficiency, but earth-abundant and cheap. We did this by investigating the structural transformations of MOS₂ at the atomic scale, so that all of the materials parts that were ‘dead’ can now work to make H₂ [hydrogen].”
The rind of an orange
in what sense were the parts “dead,” one might ask?
Visualize an orange slice where only the rind of the orange is useful; the rest — the edible bulk of the orange — must be thrown away. Molly exists as a stack of flat nanostructures, like a pile of orange slices. These layers are not molecularly bolted together like a metal but instead are loose enough to slide over one another — a kind of grease, similar to the structure of graphene, and with huge internal surface areas.
But here’s the rub: While the edges of these nanostructures match platinum in their ability to catalyze hydrogen, the relative immense surface area of their sliding interiors are useless because their molecular arrangements are different from their edges. Because of this excess baggage, a commercial catalyst would require a huge amount of molly. The slender edges would work hard like Cinderella, but the stepsister interiors would just hang out, doing nothing.
Chou, who works on two-dimensional materials and their properties, thought the intent should be to get these stepsisters jobs.
Empowering the center
“There are many ways to do this,” said co-author Bryan Kaehr, “but the most scalable way is to separate the nanosheets in solution using lithium. With this method, as you pull the material apart, its molecular lattice changes into different forms; the end product, as it turns out, is catalytically active like the edge structure.”
To determine what was happening, and the best way to make it happen, the Sandia team used computer simulations generated by coauthor Na Sai from the University of Texas at Austin that suggested which molecular changes to look for. The team also observed changes with the most advanced microscopes at Sandia. including the FEI Titan, an aberration-corrected transmission electron microscope able to view atoms normally too small to see on most scopes.
“The extended test period made possible by the combined skills of our group allowed the reactions to be observed with the amount of detail needed,” said Chou.
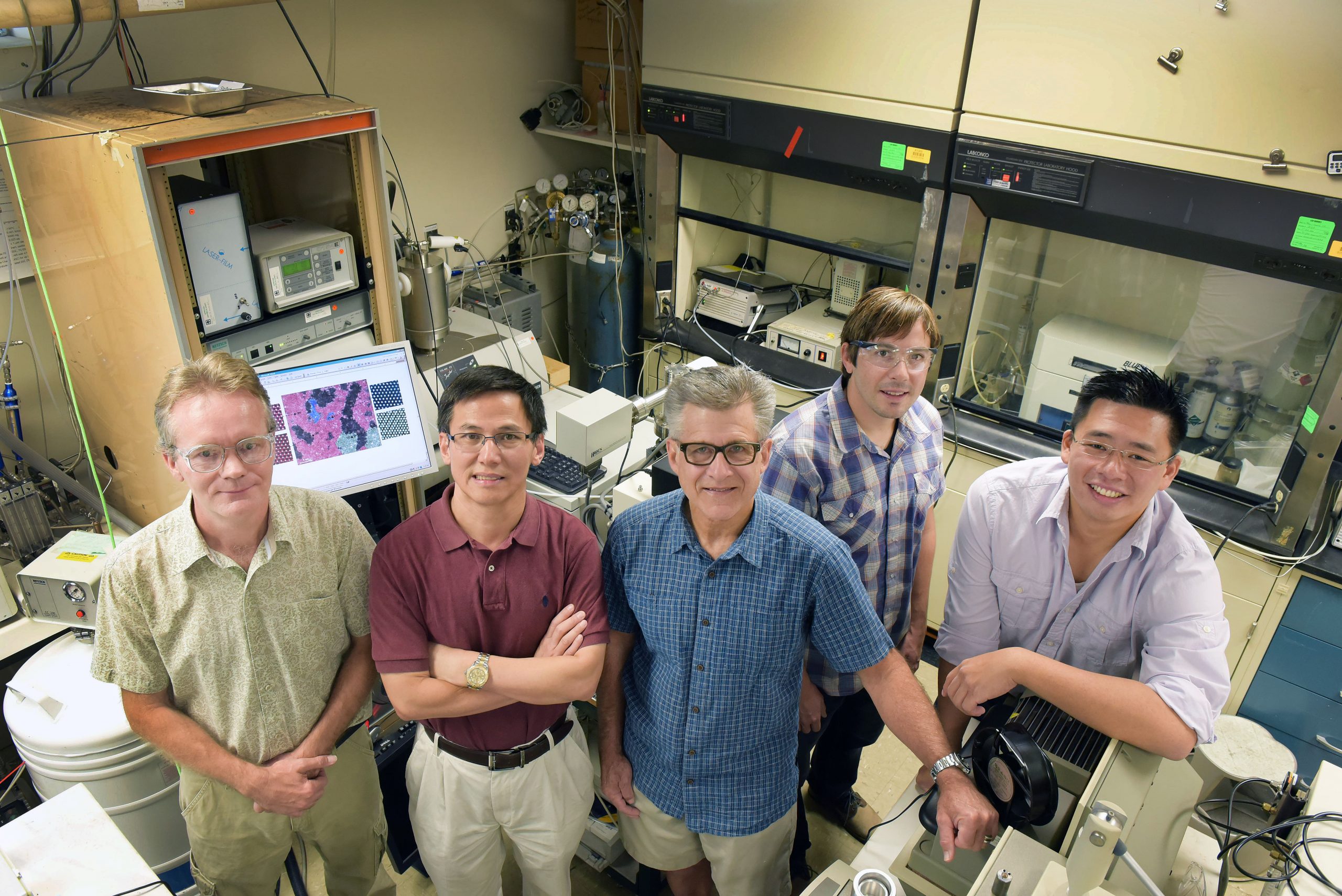
Lacking these tools, researchers at other labs had ended their tests before the reaction could complete itself, like a cook taking sugar and water off the stove before syrup is produced, resulting in a variety of conflicting intermediate results.
Ending confusion
“Why Stan’s work is impactful is that there was so much confusion as to how this process works and what structures are actually formed,” said Kaehr. “He unambiguously showed that this desirable catalytic form is the end result of the completed reaction.”
Said Sandia Fellow and University of New Mexico professor Jeff Brinker, another paper author, “People want a non-platinum catalyst. Molly is dirt cheap and abundant. By making these relatively enormous surface areas catalytically active, Stan established understanding of the structural relation of these two-dimensional materials that will determine how they will be used in the long run. You have to basically understand the material before you can move forward in changing industrial use.”
Kaehr cautions that what’s been established is a fundamental proof of principle, not an industrial process. “Water splitting is a challenging reaction. It can be poisoned, stopping the molly reaction after some time period. Then you can restart it with acid. There are many intricacies to be worked out.
“But getting inexpensive molly to work this much more efficiently could drive hydrogen production costs way down.”
‘Green’ inorganic photosynthesis
Not requiring electricity to prompt the reaction may be convenient in some circumstances and also keep costs down.
“A molly catalyst is essentially a ‘green’ technology,” said Chou. “We used sunlight for the experiment’s motive power. The light is processed through a dye, which harvests the light. A photocatalytic process stores that energy in the chemical bonds of the liberated hydrogen molecule.
“It’s photosynthesis, but using inorganic materials rather than plants,” Chou continued. “Plants use enzymes powered by sunlight to break up water into hydrogen and oxygen in a delicate process. We’re proposing a similar thing here, but in a more rapid reaction and with sturdier components.”
Kaehr said, “You could generate hydrogen and use it whenever. Hydrogen doesn’t lose charge over time or suffer from conversion inefficiencies as do batteries in a solar car.”
Other paper authors were Ping Lu, Eric Coker, Sheng Liu and Ting Luk, all from Sandia Labs, and Kateryna Artyushkova from the University of New Mexico.
The work was supported by the Department of Energy’s Office of Science, and through its user facilities at the Sandia/Los Alamos-run Center for Integrated Nanotechnologies and National Energy Research Scientific Computing Center. The Texas Advanced Computing Center also added value.