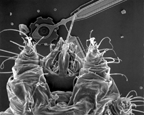
In the past two years, a succession of increasingly powerful micromachines have been developed by a team of Sandia researchers. Now they’ve made smart ones.
A smart micromachine is better than a dumb one, just as a car with gas indicator, speedometer, and cruise control is easier on a driver than one that merely runs.
An intelligent micromachine can signal for more power, communicate that it is operating too fast or slow, or even perform actions on an automated basis.
Machines of this kind — tiny motors fabricated along with integrated circuit “brains” on individual silicon chips — now have been mass produced for general applications by Sandia researchers.
The compact design, made possible by sinking the motors in tiny etched trenches, enables the fabrication of entire electromechanical systems on a chip.
“This is definitely a substantial advance they’ve come up with,” said Roger Howe, director of the University of California – Berkeley’s Sensor and Actuator Center. “A lot of people are champing at the bit to access this technology. We hope to be early in getting adapted so that talented graduate students — not just in Berkeley but anywhere in the country — can invent new circuits to play around with. Once the process is tuned up, there’s no shortage of people who will dive in to try it out.”
Said Richard Payne, director of the advance accelerometer team at Analog Devices, the largest producer of automated airbag sensors in the U.S., in Wilmington, Mass., “We’re talking with Sandia in a preliminary way to use their technology to prototype devices. The technology they’ve recently demonstrated is what we’re working on. It’s the right direction.” Analog Devices interleaves the steps of circuit and microsensor creation on a single chip, but focuses on the application of airbag accelerometers.
“This will be a big enabler for a variety of new products to be produced that are small, smart and cheap,” said Paul McWhorter, manager of the effort in Sandia’s Microelectronics Development Laboratory. By using the semiconductor industry’s fabrication methods, “We’ve created a generic manufacturing process.”
Medical possibilities include the creation of tiny drug- delivery devices. Other possibilities for the general-purpose process include the creation of tiny, inexpensive, long-lasting gyroscopes for civilian and military uses.
The process was developed to enhance the safety and security of nuclear weapons by providing smarter, more reliable locks for the devices.
How to make an intelligent micromachine
The Sandia process etches tiny trenches in silicon chips and fabricates the machines within these depressions like pool tables in sunken living rooms. The machines, heat-treated, are then submerged — like the Alpine Iceman, preserved in the interior of a glacier — in a tiny hardening sea of silicon dioxide.
“If you first sink the machine in a trench and then fill in around it, in effect you’ve recreated a pristine wafer for doing electronic processing,” said Steve Montague, inventor of the approach.
The hardened silicon dioxide re-creates a level chip surface upon which circuitry is fabricated by photolithography.
Removal of the silicon dioxide at the end of the process frees the microengines.
Working systems are manufactured with a 78 percent success rate — a reasonably high measure of production yield.
The process can produce a wide range of micromachine systems because it allows independent optimization of micromachine and microcircuit performances, achieving the “paradoxical but desirable result of larger, more powerful micromachines with smaller transistors,” said McWhorter.
While the machines and electronics now are completely fabricated at Sandia, another option is to continue fabrication of the machines and chips at the Labs’ Microelectronic Development Laboratory but permit novel circuitry to be added at other integrated circuit facilities. An effort also is underway to transfer the technology to industrial partners for large scale production.
The inexpensive manufacturing process can be used either to produce “tens of thousands of units a day, reducing costs significantly for government or industrial users, or to do specialty work making unique motors and circuits for university or medical researchers,” Sandia scientist Jeff Sniegowski said.
Circuits fabricated only microns from a machine eliminate ghost signals — parasitic currents — created by excess electrical capacitance in long connecting wires.
“Without this interference, by applying a mechanical load you can measure the capacitance change in the drive gear teeth as they move in and out,” said Sandia engineer Ernest Garcia. “Then you know how fast the machine is moving. The sequence allows you to understand velocity.”
Past difficulties and successes in building micromachines
The difficulty with joining a microcircuit to a micromachine on a silicon chip has been that aluminum circuit interconnectors, if formed first, melt when the micromachines are heat-treated. (If the gears are not heated to approximately 900 degrees Centigrade, said Sandia scientist Jeff Sniegowski, “Like potato chips, they curl.”)
If micromachines are fabricated first, their elevation above the chip surface creates bumps that distort the delicate process of etching accurate microcircuits. “You can’t have fine undulations or striations in the photoresist,” Sniegowski said. “At that scale, five microns is a mountain, and a micromachine is five to six microns high.”
Analog Devices was one of the first to demonstrate the advantage of integrating micromachines and electronics. Even earlier work by Roger Howe in the mid-1980s at UC Berkeley served as a motivation for the Sandia work. Howe chose to build the circuits first but make the interconnected circuit wiring of tungsten, which resists heat better than the cheaper industry standard of aluminum.
Background
Sandia micromachines are approximately one millimeter square. The machines currently are embedded in chip trenches six microns deep, producing a single level structure suitable for accelerometers and other sensors. Three-level structures have been fabricated to a depth of 18 microns. These are capable of turning external gearing and are completely compatible with the new integrated technique.
The advance is the latest in a series by Sandia scientists. Last September, the Laboratories announced that its researchers – – using methods similar to those of the integrated circuit fabrication industry — had succeeded in mass producing micromachines that could perform work. The machines turn gears each one-hundredth the weight of a dust mite — itself seen by the human eye as a tiny dot — at hundreds of thousands of revolutions per minute. Each gear is approximately one hundredth the thickness of a sheet of paper, and smaller in diameter than a human hair. The advance was selected as one of the five best technological innovations of the year by the magazine Industry Week.
In 1994, Sandia researchers announced the creation of a micro-steam engine; however, modern day microdevices that produce enough output to do work are powered by electrostatic forces.