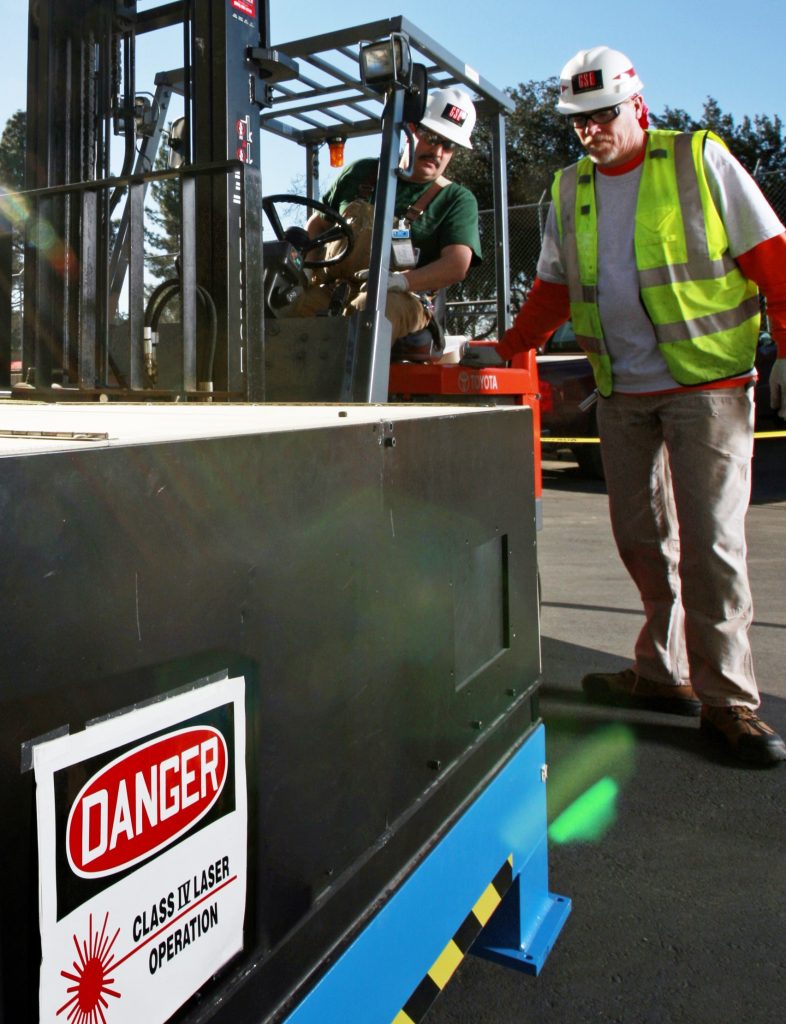
LIVERMORE, Calif. — Las Positas College, located just a few short miles away from the Sandia/California campus, might be a close partner of Sandia’s in the near future as the lab continues to pursue academic and industry collaborators on its new open campus. But even with an eye to the future, this same college now possesses a piece of the lab’s history.
Sandia has successfully transferred its original LENS® machine to Las Positas College for use in the college’s welding department. LENS, or Laser Engineered Net Shaping, is a modern technique that can fabricate three-dimensional, prototype metallic parts out of virtually any metal alloy.
Sandia’s John Smugeresky, a co-developer of the device along with former Sandian David Keicher, calls the machine “a kind of a precursor to the replicator from Star Trek lore,” a 3-D copy machine of sorts popularized on the long-running film and television series.
The serial number of the transferred unit is 001, signifying that it was the first one ever manufactured. The equipment was moved to Las Positas through the Department of Energy (DOE) Energy-Related Laboratory Equipment (ERLE) program, which grants available excess or used energy-related laboratory equipment to educational facilities for use in energy-oriented education programs.
Despite being manufactured in 1994, the inaugural LENS machine uses the same technology as present-day machines deployed commercially around the world.
“The technology is not antiquated at all and continues to be used in metallurgy and microstructure evaluation, as a metal-joining technique, and as a research tool,” said Smugeresky.
For years, he said, the LENS machine was used for the lab’s nuclear weapons (NW) mission, specifically to help designers create prototype parts for safety and security upgrades, and to manufacture replacement parts for existing NW systems. The National Nuclear Security Administration (NNSA) Office of Stockpile Technology sponsored the LENS machine’s official process qualification in 2006 through a project titled “Qualification of LENS for the Repair and Modification of NWC Metal Components.” Process qualification gives engineers and other LENS users the needed confidence to specify LENS as the primary tool for fabrication, repair or modification of their components.
The LENS machine features a glove box (to control contamination of materials), a high-powered laser, mirrors and powder feeders. The process fabricates metal parts directly from the Computer-Aided Design (CAD) solid models using metal powder particles injected into a molten pool created by the focused, high-powered laser beam. The technology was licensed years ago by the Albuquerque-based company Optomec (where Keicher now serves as vice president and chief technology officer).
Las Positas welding instructor Scott Minor plans to utilize the LENS machine to introduce students to metal joining techniques.
“We look forward to seeing the equipment being used to inspire future welders, technicians and engineers for the careers of tomorrow,” said Minor. “It is partnerships like this one between Las Positas College and Sandia that make our educational experience more meaningful to the student and help them look forward to careers, materials and process that will be part of tomorrow’s industry.” He said the LENS machine should help the college’s efforts to change the traditional image of welding from “grimy leather, hard hats, steel shoes and a dirty environment” to one of sophistication and cutting-edge technology.
Sandia plans to add value to the equipment transfer by developing opportunities for its technical staff to work directly with Las Positas students.
“The transfer provides a specific focus for interaction between volunteer technical staff at Sandia and the dedicated educators at Las Positas,” said Tom Felter, manager of Sandia’s hydrogen and metallurgy science group.
Sandia continues to explore other partnerships with Las Positas, particularly as the Livermore Valley Open Campus (LVOC) initiative unfolds.