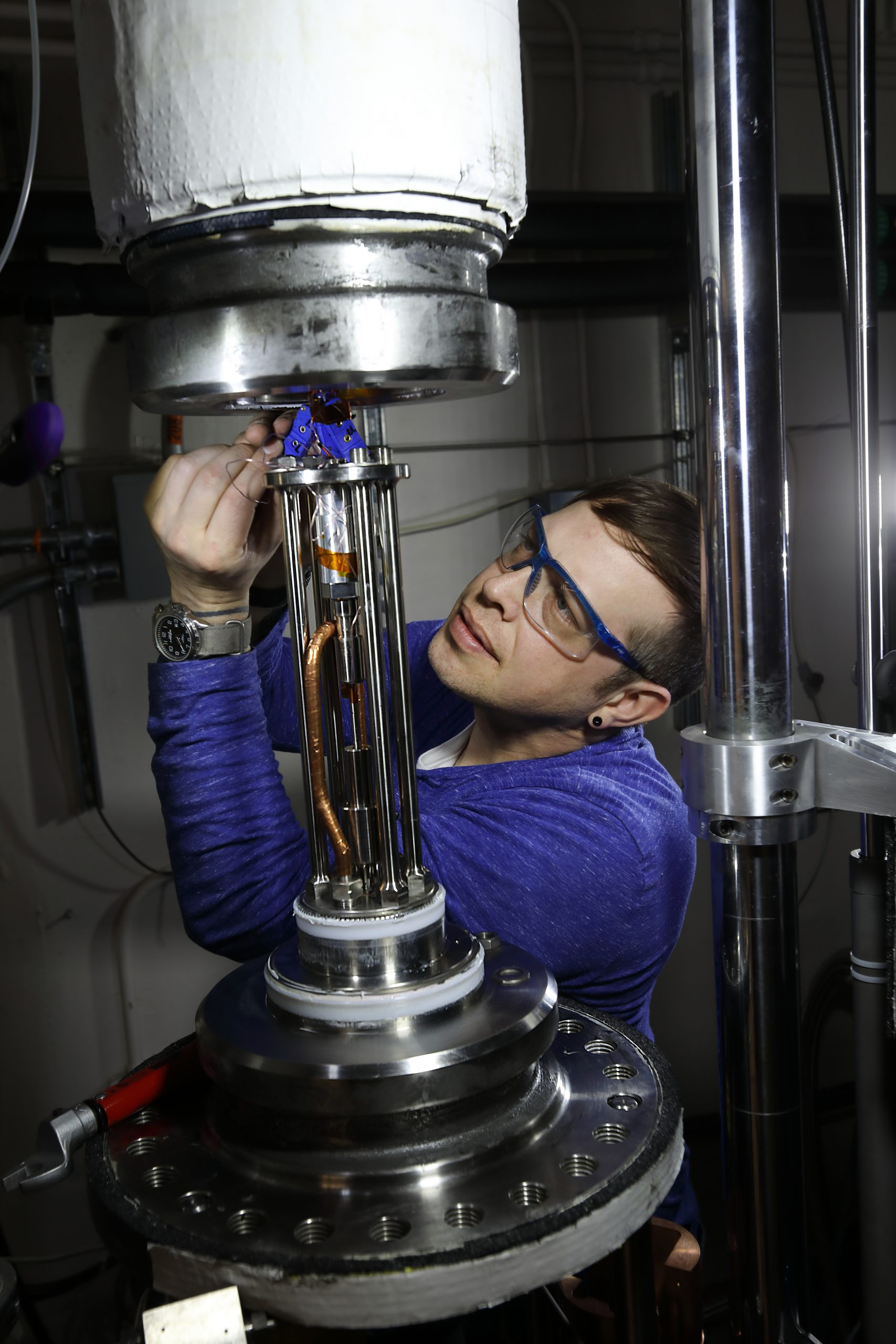
LIVERMORE, Calif. — Researchers at Sandia and Pacific Northwest national laboratories are leading a collaborative effort to investigate how hydrogen affects materials such as plastics, rubber, steel and aluminum.
The Hydrogen Materials Compatibility Consortium, or H-Mat, will focus on how hydrogen affects polymers and metals used in diverse sectors including fuel cell transportation and hydrogen infrastructure. Researchers at Oak Ridge, Savannah River and Argonne national laboratories, as well as in industry and academia, are also part of the collaboration. The effort supports the U.S. Department of Energy H2@Scale initiative, which aims to advance hydrogen utilization for energy production and storage as well as industrial processes.
“The advanced computational capabilities, unique experimental facilities and scientific expertise at the national laboratories will provide enhanced understanding of the interactions of hydrogen gas with polymers and metals,” said Chris San Marchi, Sandia materials scientist and co-lead for the consortium. “The goal is to improve materials reliability in hydrogen infrastructure for large scale use of hydrogen as an energy carrier.”
Imaging across dimensions
Today, the United States produces about 10 million metric tons of hydrogen every year, primarily for petroleum refining and ammonia production. Hydrogen demand is growing in transportation, where thousands of fuel cells are used in in forklifts and vehicles. Hydrogen applications are also emerging through innovation in additional sectors, such as iron refining and energy storage.
Current metal structures that contain hydrogen, such as valves, fuel tanks and storage vessels, are manufactured from several expensive alloys of aluminum and steel. In such materials, hydrogen interacts with their atomic make-up in ways that can introduce damage. Components are routinely inspected and taken out of service after a set number of years so that this damage does not result in unexpected failures. Since the mechanisms of interactions between hydrogen and materials at the nano and microscales are not well understood, the lifetimes of various components are challenging to estimate. Even less is known about how hydrogen affects the structure and mechanical properties of polymers, such as plastic pipes and rubber seals.
To date, much of the existing hydrogen infrastructure has been informed by research performed at the national labs to characterize metals and polymers in high-pressure hydrogen environments. The H-Mat consortium seeks to dig deeper into the underlying science of this behavior, by using advanced imaging and surface characterization techniques to study hydrogen interactions with materials at size scales ranging from the atomistic to the engineering scale. Researchers are also developing computer models to predict the mechanisms of these interactions and the evolution of hydrogen-induced damage. Those predictions can then help materials scientists tailor the compositional and microstructural makeup of materials to withstand hydrogen-induced damage.
Microscopic mechanisms of degradation
Hydrogen affects metals through a class of interactions called hydrogen embrittlement. Hydrogen embrittlement and hydrogen-induced cracking in metals can be visible to the naked eye. But these cracks start with interactions between hydrogen and a material at lengths a thousand times less than the width of a human hair. Little is known about the effects of hydrogen at these tiny lengths.
Far less is known about how hydrogen affects polymers. For these materials, hydrogen can form pressurized gas bubbles that concentrate stress and lead to damage. There is growing evidence that hydrogen also interacts with polymers at the atomic scale, which may enhance degradation mechanisms.
Researchers at Sandia are studying the behavior of metals and polymers while exposed to high-pressure hydrogen environments using unique equipment at the Livermore campus, while the team at Pacific Northwest National Lab leads the characterization and experimental studies of cracking and degradation in polymers.
“Materials scientists at the two labs are the foundation for the experimental studies within this consortium,” says Kevin Simmons, the PNNL senior research scientist who serves as H-Mat co-lead. “We’re also leveraging our labs’ high-performance computational capabilities to study fundamental hydrogen-materials interactions.”
Researchers at collaborating labs provide expertise in advanced imaging and additional high-performance computing. Existing and new academic, industrial and institutional partnerships bring knowledge about material needs for specific infrastructure applications, and non-proprietary data will be made public to accelerate research and development.