ALBUQUERQUE, N.M. — Word of an extraordinarily inexpensive material, lightweight enough to protect satellites against debris in the cold of outer space, cohesive enough to strengthen the walls of pressurized vessels experiencing average conditions on Earth and yet heat-resistant enough at 1,500 degrees Celsius or 2,732 degrees Fahrenheit to shield instruments against flying debris, raises the question: what single material could do all this?
The answer, found at Sandia National Laboratories, is sweet as sugar.

That’s because it is, in fact, sugar — very thin layers of confectioners’ sugar from the grocers, burnt to a state called carbon black, interspersed between only slightly thicker layers of silica, which is the most common material on Earth, and baked. The result resembles a fine layer cake, or more precisely, the organic and inorganic layering of a seashell, each layer helping the next to contain and mitigate shock.
“A material that can survive a variety of insults — mechanical, shock and X-ray — can be used to withstand harsh environmental conditions,” said Sandia researcher Guangping Xu, who led development of the new coating. “That material has not been readily available. We believe our layered nanocomposite, mimicking the structure of a seashell, is that answer.”
Most significantly, Xu said, “The self-assembled coating is not only lightweight and mechanically strong, but also thermally stable enough to protect instruments in experimental fusion machines against their own generated debris where temperatures may be about 1,500 C. This was the initial focus of the work.”
“And that may be only the beginning,” said consultant Rick Spielman, senior scientist and physics professor at the Laboratory for Laser Energetics at the University of Rochester, credited with leading the initial design of Sandia’s Z machine, one of the destinations for which the new material is intended. “There are probably a hundred uses we haven’t thought of.” He envisions possible electrode applications delaying, rather than blocking, surface electron emissions.
Aiding the nuclear survivability mission
The coating, which can be layered on a variety of substrates without environmental problems, was the subject of a Sandia patent application in June 2021, an invited talk at a pulsed power conference in December 2021 and again in a recent technical article in MRS Advances, of which Xu is lead author.
The work was done in anticipation of the increased shielding that will be needed to protect test objects, diagnostics and drivers inside the more powerful pulsed power machines of the future. Sandia’s pulsed-power Z machine — currently the most powerful producer of X-rays on Earth — and its successors will certainly require still greater debris protection against forces that could compare to numerous sticks of dynamite exploding at close range.
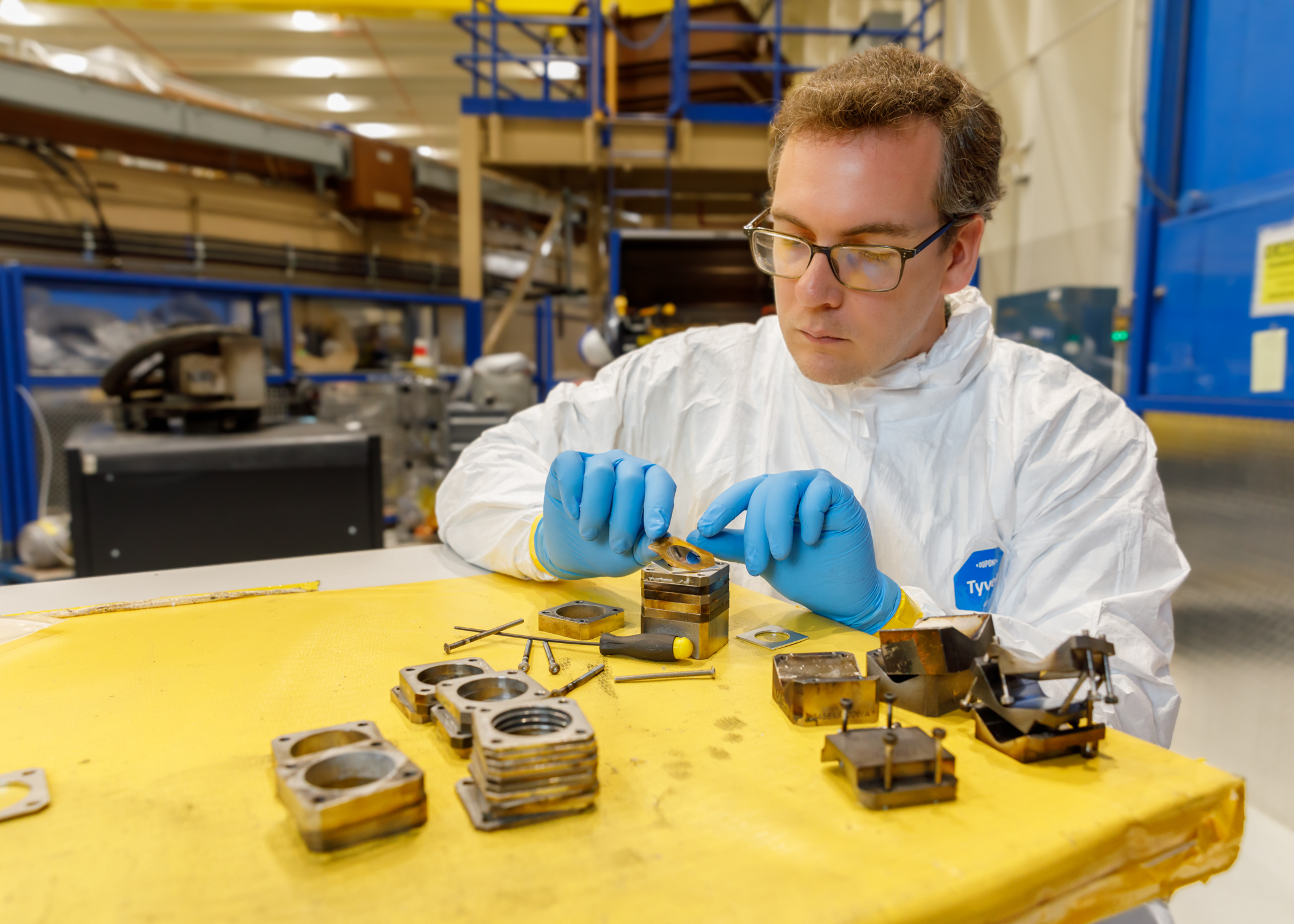
“The new shielding should favorably impact our nuclear survivability mission,” said paper author and Sandia physicist Chad McCoy. “Z is the brightest X-ray source in the world, but the amount of X-rays is only a couple percent of the total energy released. The rest is shock and debris. When we try to understand how matter — such as metals and polymers — interacts with X-rays, we want to know if debris is damaging our samples, has changed its microstructure. Right now, we’re at the limit where we can protect sample materials from unwanted insults, but more powerful testing machines will require better shielding, and this new technology may enable appropriate protection.”
Other, less specialized uses remain possibilities.
The inexpensive, environmentally friendly shield is light enough to ride into space as a protective layer on satellites because comparatively little material is needed to achieve the same resilience as heavier but less effective shielding currently in use to protect against collisions with space junk. “Satellites in space get hit constantly by debris moving at a few kilometers per second, the same velocity as debris from Z,” McCoy said. “With this coating, we can make the debris shield thinner, decreasing weight.”
Thicker shield coatings are durable enough to strengthen the walls of pressurized vessels when added ounces are not an issue.
Dramatic cost reduction anticipated
According to Guangping, the material cost to fabricate a 2-inch diameter coating of the new protective material, 45 millionths of a meter and microns thick, is only 25 cents. In contrast, a beryllium wafer — the closest match to the thermal and mechanical properties of the new coating, and in use at Sandia’s Z machine and other fusion locations as protective shields — costs $700 at recent market prices for a 1-inch square, 23-micron-thick wafer, which is 3,800 times more expensive than the new film of same area and thickness.
Both coatings can survive temperatures well above 1,000 C, but a further consideration is that the new coating is environmentally friendly. Only ethanol is added to facilitate the coating process. Beryllium creates toxic conditions, and its environs must be cleansed of the hazard after its use.
How testing proceeded
The principle of alternating organic and inorganic layers, a major factor in seashell longevity, is key to strengthening the Sandia coating. The organic sugar layers burnt to carbon black act like a caulk, said Sandia manager and paper author Hongyou Fan. They also stop cracks from spreading through the inorganic silica structure and provide layers of cushioning to increase its mechanical strength, as was reported 20 years ago in an earlier Sandia attempt to mimic the seashell mode.
Greg Frye-Mason, Sandia campaign manager for the Assured Survivability and Agility with Pulsed Power, or ASAP, Laboratory Directed Research and Development mission campaign funding the research, initially had his doubts about the carbon insertion.
“I thought that the organic layers would limit applicability since most degrade by 400 to 500 C,” he said.
But when the carbon-black concept demonstrated robustness to well over 1,000 C, the positive result overcame the largest risk Frye-Mason saw as facing the project.
Seashell-like coatings initially tested at Sandia varied between a few to 13 layers. These alternating materials were pressed against each other after being heated in pairs, so their surfaces crosslinked. Tests showed that such interwoven nanocomposite layers of silica with the burnt sugar, known as carbon black after pyrolysis, are 80% stronger than silica itself and thermally stable to an estimated 1,650 C. Later sintering efforts showed that layers, self-assembled through a spin-coating process, could be batch-baked and their individual surfaces still crosslinked satisfactorily, removing the tediousness of baking each layer. The more efficient process achieved very nearly the same mechanical strength.
(Graphic by Alicia Bustillos and data provided by Hongyou Fan and Guangping Xu)
Research into the coating was funded by ASAP to develop methods to protect diagnostics and test samples on Z and on next-generation pulsed power machines from flying debris.
“This coating qualifies,” Frye-Mason said.