ALBUQUERQUE, N.M. — Three years of design, planning and preparation came down to a split second, a loud boom and an enormous splash in a successful impact test of hardware in the nose assembly of an unarmed, mock B61-12 nuclear bomb.
The Sandia National Laboratories test also captured data that will allow analysts to validate computer models of the bomb, part of Sandia’s decade-long effort in the B61-12 Life Extension Program (LEP). An LEP is a way to extend the life of an aging weapon without adding new military capability. The B61-12 LEP is an $8.1 billion National Nuclear Security Administration (NNSA) program coordinated across the nation’s nuclear security enterprise. Sandia is working with the NNSA, the program lead, and five NNSA partner sites, industry partners and the U.S. Air Force, the B61-12 customer.
The test, the first of three with Sandia’s cannon-like Davis gun, shot the assembly and its diagnostics into an 8-foot-deep steel-reinforced concrete water tank with a soil-filled bunker underneath to capture the hardware. The packed-dirt bunker makes it easier for engineers to recover data recorders and reusable parts and ensures that a test piece isn’t damaged.
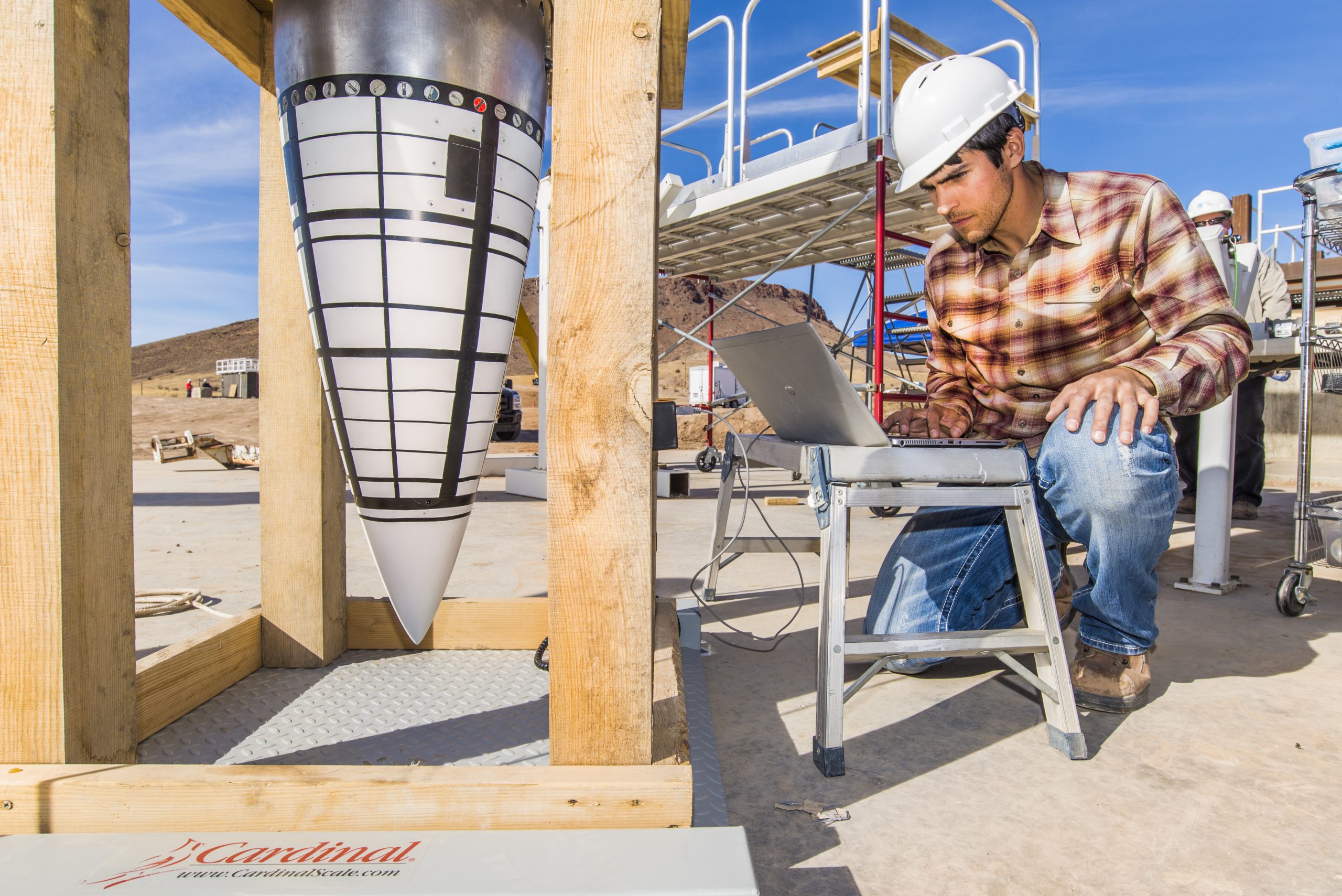
The tests were designed to validate a systems requirement for the B61-12 and represented a worst-case scenario: a slow velocity into a soft target, in this case, 10,500 gallons of water. Shots were set for a prescribed velocity and angle to validate the impact sensor response for ground fuzing and to help understand the design margin, said Tyler Keil, lead engineer for the B61-12 Davis gun test series.
Keil and more than a dozen colleagues who worked on the test watched the Jan. 28 shot from a hill a half-mile from the mobile Davis gun, stationed at New Mexico Tech’s Energetic Materials Research & Testing Center (EMRTC) in the hills west of the Socorro campus.
‘Awesome’ test highlighted years of work
“It was awesome,” Keil said after the shot. Keil, who worked toward the test for more than three years, brought team members to EMRTC so they could watch a highlight of their work: shooting a mock bomb out of the gun. Waning sunlight meant waiting until the next day to recover test data, and Keil joked he’d “determine how happy I really am” after seeing that data.
The Davis gun series marked the end of testing for the nose design, and by the end of the week, Keil knew the test had captured what the team needed. “Our team will assess these data, make note of any findings we see where improvements are needed to meet requirements, brainstorm ideas to address the findings and incorporate them into the next design,” Keil said. “We’ll then repeat the tests on the new design to verify that the changes were successful.”
Manager Doug Dederman, whose department conducted the test, explained how the gun works: Imagine the barrel as a straw, open at both ends, with an explosive charge sandwiched between the test nose assembly and a 2,000-pound steel slug, called the reaction mass. The test component and reaction mass are simultaneously blown out opposite ends of the barrel, the test piece slamming into the water of the adjacent pool and underlying bunker, and the reaction mass arcing to land behind a small hill.Using a reaction mass eliminates the recoil load in the gun chassis during firing.
Crews from Sandia and EMRTC spent most of two days in final test preparations. On test day, the nose assembly, mounted on an aluminum tube to replicate the B61-12 body, sat in a stand about 200 yards from the pool. There it waited until time to load it into the 40-foot long, 16-inch diameter barrel of the white Davis gun, stark against the backdrop of blue sky and a red jagged volcanic hill.
It took more than 20 minutes to move the projectile with the attached nose assembly from the stand to the gun. The crew removed the assembly stand brackets, then suspended the projectile from the tines of a forklift equipped with a long hydraulic boom. They steadied the projectile with tag lines as the forklift driver maneuvered up a dirt ramp to the Davis gun. There, it was bracketed into another stand to hold and roll it under the barrel where it was attached to a threaded rod and drawn up into the vertical barrel. The gun’s dual-sheave hoisting system minimized rotation as the projectile was lifted into position in the barrel.
Capturing footage from the test
High-speed cameras positioned at three levels in window ports in a hut on one side of the pool and flash bulbs in a hut on the other side were synchronized with the gun’s explosive charge to catch the action underwater.
As the arming and firing crew finished final preparations, everyone else evacuated to the viewing area for safety. The gun — which can be set at any angle — was tilted to firing position, the end with the nose piece pointed toward the pool. The crew at the gun finished local arming preparations and drove to the remote gun firing trailer below the hill at the viewing area. A roll call assured that everyone was accounted for and away from the test site. The gunner announced “Charged,” counted down “five, four, three, two, one” and fired the gun just before 4 p.m.
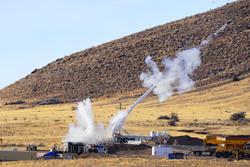
Water splashed into the air as the nose assembly hit the pool and a cloud of smoke drifted from the raised end as the reaction mass flew behind a hill well away from the action and the observers. “The reaction mass landed just where we expected it to, a first indication that we are close to the velocity we wanted,” Keil said.
Once the firing crew gave the all-clear, onlookers returned to the site and climbed onto the steel platform around the pool. Water had splashed a large radius of the dirt clearing around the pool, and the rest drained into a ramp leading down to the bunker. A large plastic tube dropped into the ramp with an attached fireman’s hose siphoned the remaining water toward a nearby arroyo while a member of the crew shoveled mud out of the bunker to locate the test piece for the next day’s excavation.
About an hour after the firing, a small convoy of vans and pickups drove back across a winding dirt road through the hills to EMRTC headquarters. Some of the crew would be back the next day to recover the data recorders so engineering analysts could begin their work. Analysts will spend the next year using the data to calibrate their models, then explore impact scenarios that weren’t tested to evaluate the impact sensor’s performance.
“The B61-12 LEP has performed several impact tests of various target types and velocities over the last year to verify its ground fuzing performance,” Keil said. “The Davis gun test series specifically tests the B61-12 ground fuzing performance during a water impact. All of the impact testing contributes to how reliably the B61-12 will fuze upon a ground impact.”
For more images of the Davis gun impact test, visit Sandia’s Flickr site.