ALBUQUERQUE, N.M. — When a small business needed help proving that its invention, a tabletop laser system, could characterize metals faster and more easily than current equipment, they turned to Sandia National Laboratories’ expertise in metals characterization.
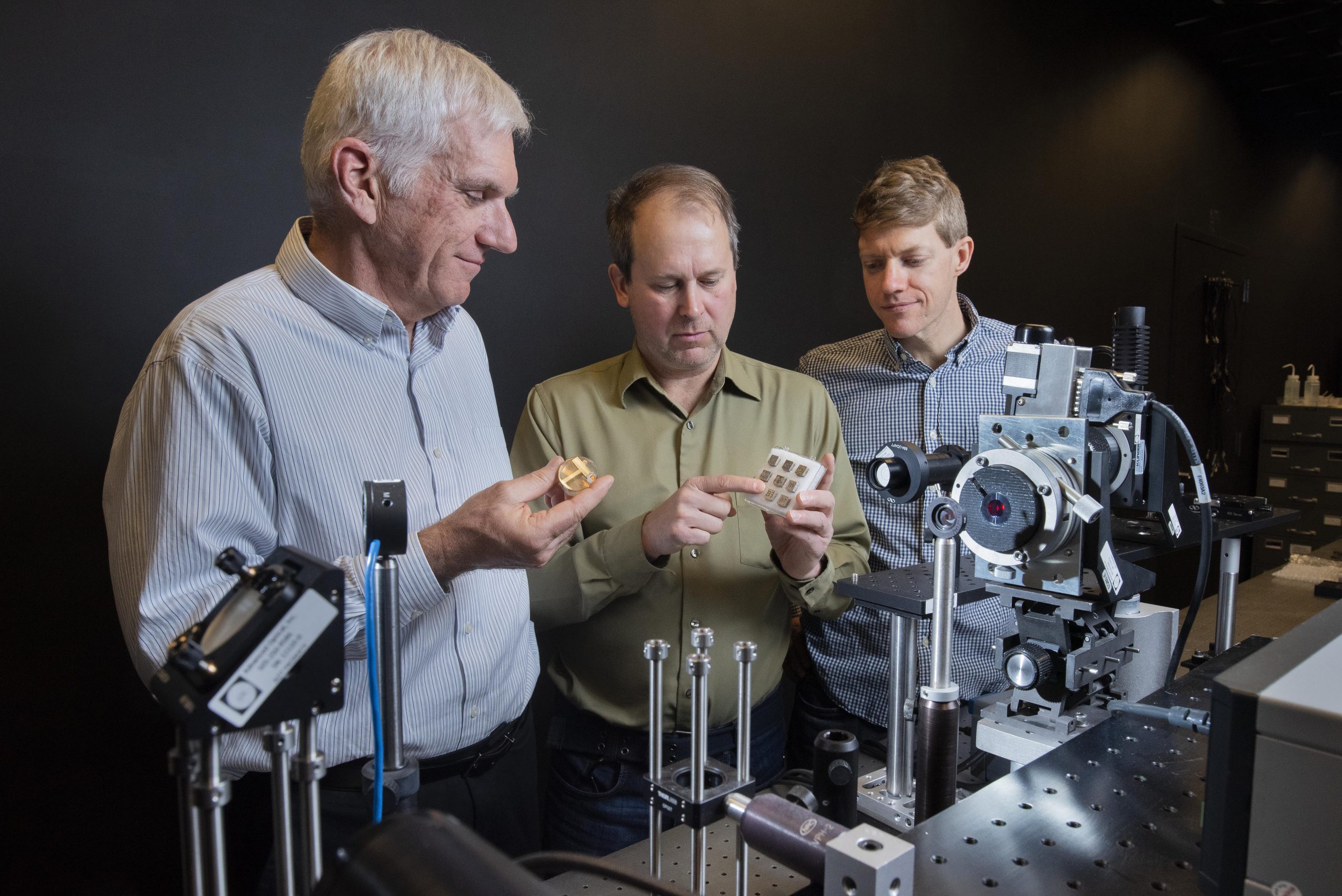
Sandia’s testing verified that Albuquerque-based Advanced Optical Technologies’ patented Crystallographic Polarization-Classification Imaging, or CPCI, process reduces time spent on characterization from hours to minutes. The new imaging process has applications in the aerospace, automotive, energy and medical industries and for 3D printing.
Sandia and Advanced Optical Technologies were matched through the New Mexico Small Business Assistance Program, which offers expertise to help solve technical challenges faced by small companies in New Mexico. This includes projects that require testing, design consultation or access to special equipment or facilities that are not available to small businesses.
Due, in part, to the results of Sandia’s study, the company received funding to build the system for the U.S. Air Force, where it primarily will be dedicated to titanium crystallography. CPCI can also characterize other metals, including beryllium, magnesium, cobalt, zinc, tin and zirconium.
The company also received New Mexico Economic Development and Office of Economic Adjustment grants with support from the New Mexico Manufacturing Extension Partnership. In addition, the partnership was recognized at a 2019 New Mexico Small Business Association Innovation Celebration.
Malini Hoover, the company’s CEO, said she is interested in marketing CPCI to companies, national labs and universities that characterize metal crystallography. Titanium is lightweight, corrosion-resistant, and can withstand extremely high temperatures — qualities that make the metal a popular choice for the aerospace industry.
Technology could streamline quality control
As the need for titanium increases with the high demand for newer, lighter military and commercial planes, manufacturers must continue to verify the metal for stress and maintain parts, Hoover said, adding that the company’s technology could streamline the quality control process.
Sandia materials scientist Joseph Michael was paired with the company for the project and conducted a test using a scanning-electron microscope, current technology that can be difficult for small businesses to access because the microscopes are large, expensive and require experts to run. Metals characterization is one of Sandia’s strengths — the labs have been doing this for many years, Michael said.
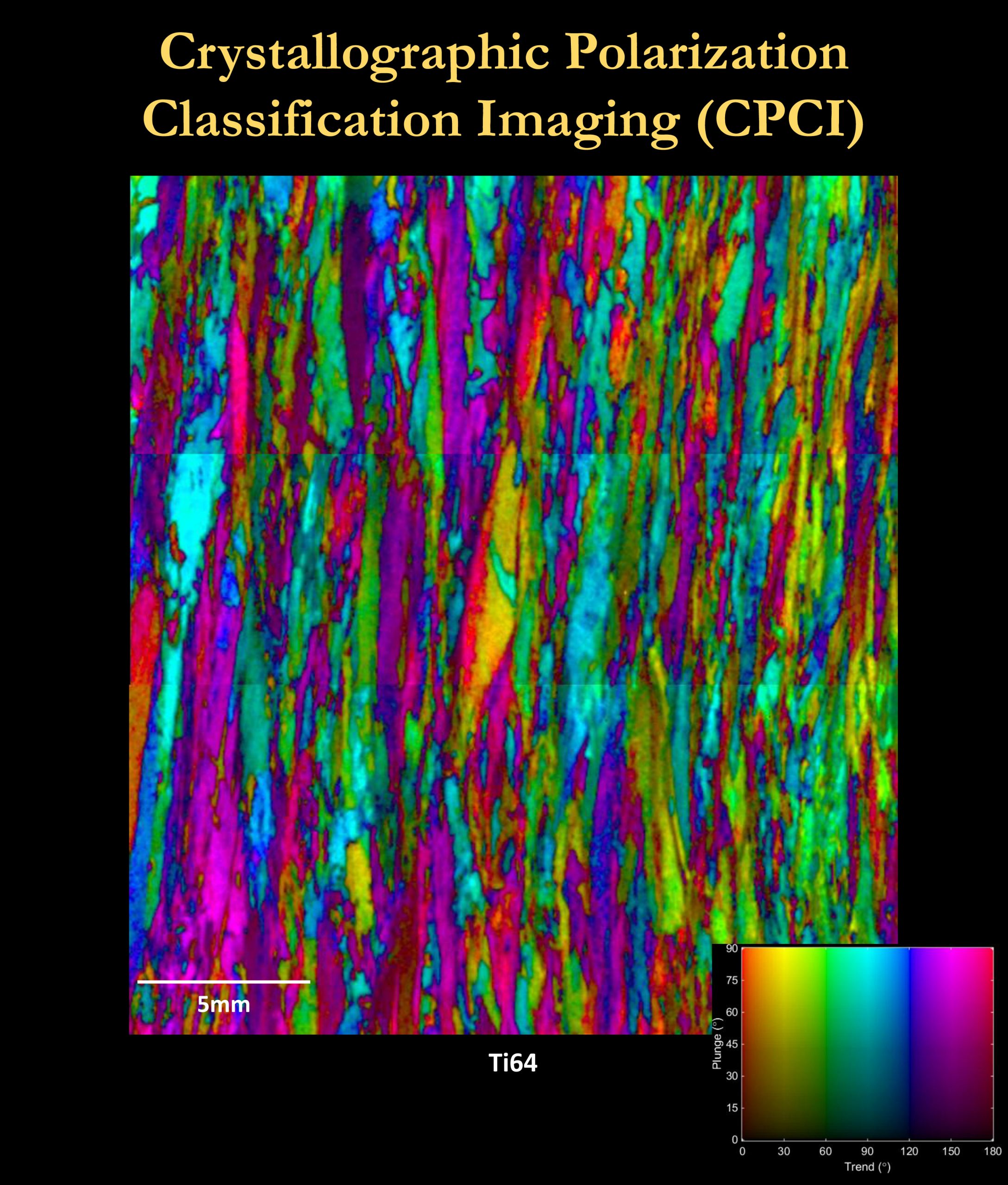
“We use scanning-electron microscopes in very sophisticated ways here, and I think that’s what was attractive to Advanced Optical Technologies,” he said.
By helping with the project, Michael said he was able to think about metal characterization in new and exciting ways.
“It’s been energizing to me to see other techniques that can do some of the things that we do in the lab in a faster, higher-throughput way,” he said. “It’s been more than neat — it’s been exciting to see it all happen. If you can generate data that gets you 90% of the solution and do it quickly from an unprepared sample, that’s a great place to be.”
Current ‘gold-standard’ technology requires destructive process
A current process for characterizing titanium is a method called electron backscatter diffraction, the test Michael provided. The process involves inserting a small sample of titanium into a scanning electron microscope that can produce images at the nanoscale, helping scientists determine a material’s melting point, color, strength and chemical reactivity.
Scanning-electron microscopes scan samples with a focused beam of electrons that interacts with the atoms in the material. This produces various signals that contain information about the surface, composition and crystallography of the sample. That information produces highly magnified images of the metal, and skilled metallurgists can make decisions about final properties of the part.
Electron backscatter diffraction is currently a gold standard in metals characterization, Michael said, but it can’t be completed during live production because the metal must be prepared using highly trained technologists and specialized equipment. This process is time-intensive and destructive because scientists have to cut a small piece of the metal to fit inside the microscope, something you can’t do to large sheets of metal or to the side of an aircraft.
Non-destructive imaging offers several benefits
With the company’s process, a titanium billet, sheet or finished part can be placed in front of the sensor to image the surface with an eye-safe laser. Because the sample doesn’t need to be inserted into a small chamber, it doesn’t need to be cut; the original piece of titanium remains whole. This makes the process non-destructive.
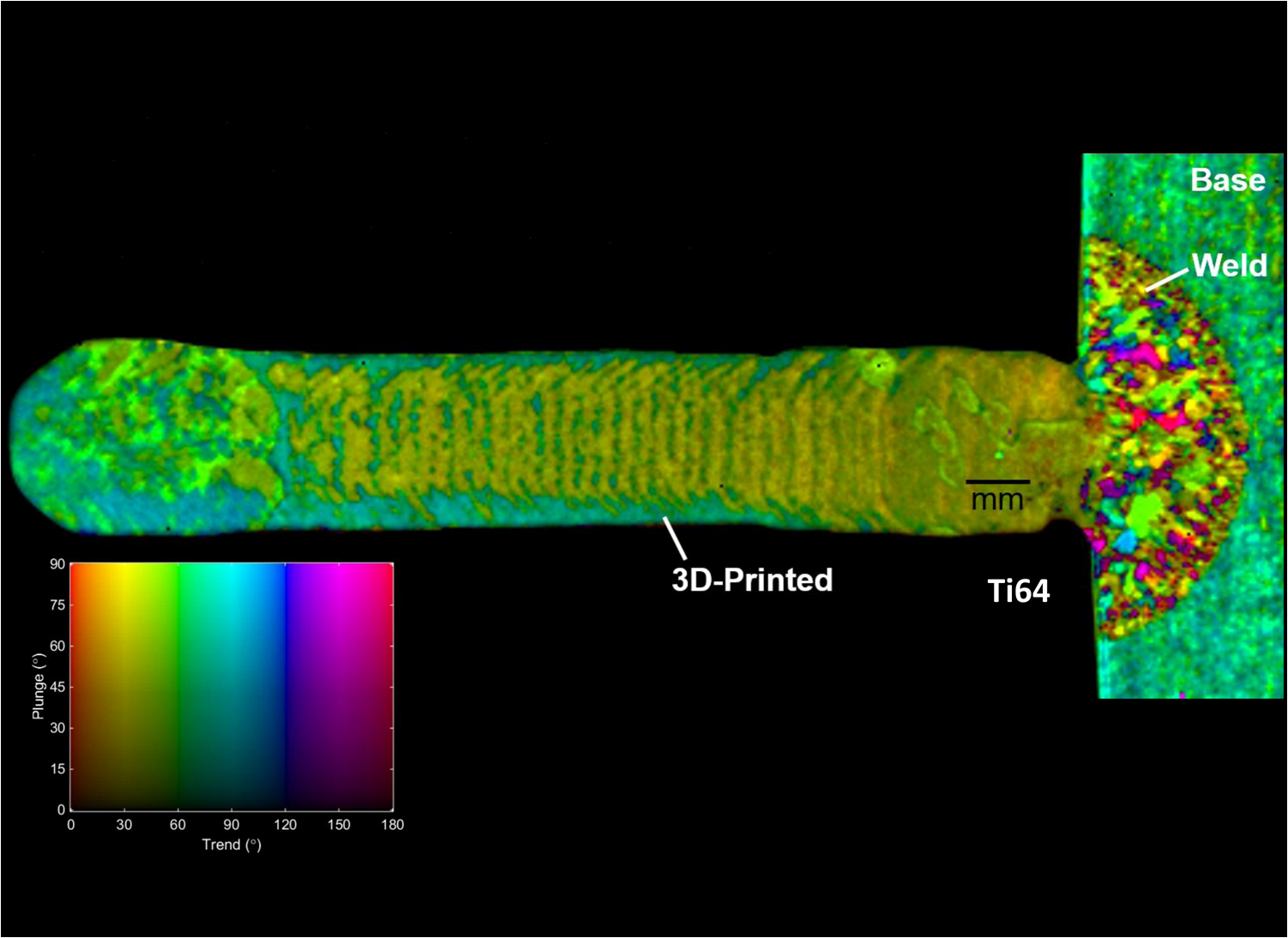
The system also produces a larger image than a scanning-electron microscope can, and because the process is standardized and operates simply by pushing a button, experts aren’t necessarily needed for the initial imaging. The process reduces labor costs and allows experts to better spend their time analyzing the images and making decisions.
This technology could potentially characterize titanium while a part is being produced, Hoover said, and the larger field of view makes it easier for experts and manufacturers to make critical decisions rapidly. It also could be used to analyze aircraft parts in service during maintenance checks. The sensor is portable enough to set up outside the plane and provide crystallographic images of parts in real time, improving flight safety.
“Currently, there is no way to check crystallography on the ground during maintenance,” Hoover said.
System has applications for many industries
The technology could also benefit companies and labs working with 3D printers, something that Michael has expressed interest in.
“Currently, 3D-printed parts require frequent inspection. Sandia is interested in inspecting 3D-printed parts.” Hoover said. “There is interest in putting a CPCI sensor in a 3D printer and inspecting layer by layer, so as soon as something is wrong, the build can be stopped or corrected.”
Hoover said this technology also could benefit the medical field for prosthetics.
“Everything in our body — spine, plates, knees, hip replacements — can be made out of titanium,” she said. “So, this technology could also be utilized in the medical field along with the other industries.”