LIVERMORE, Calif. — Researchers at Sandia National Laboratories have identified a straightforward change to the formula for radiation-detecting plastic. The change prevents “fogging,” which reduces the lifetime of the plastics used to detect nuclear material transiting through the U.S. Department of Homeland Security’s radiation detectors.
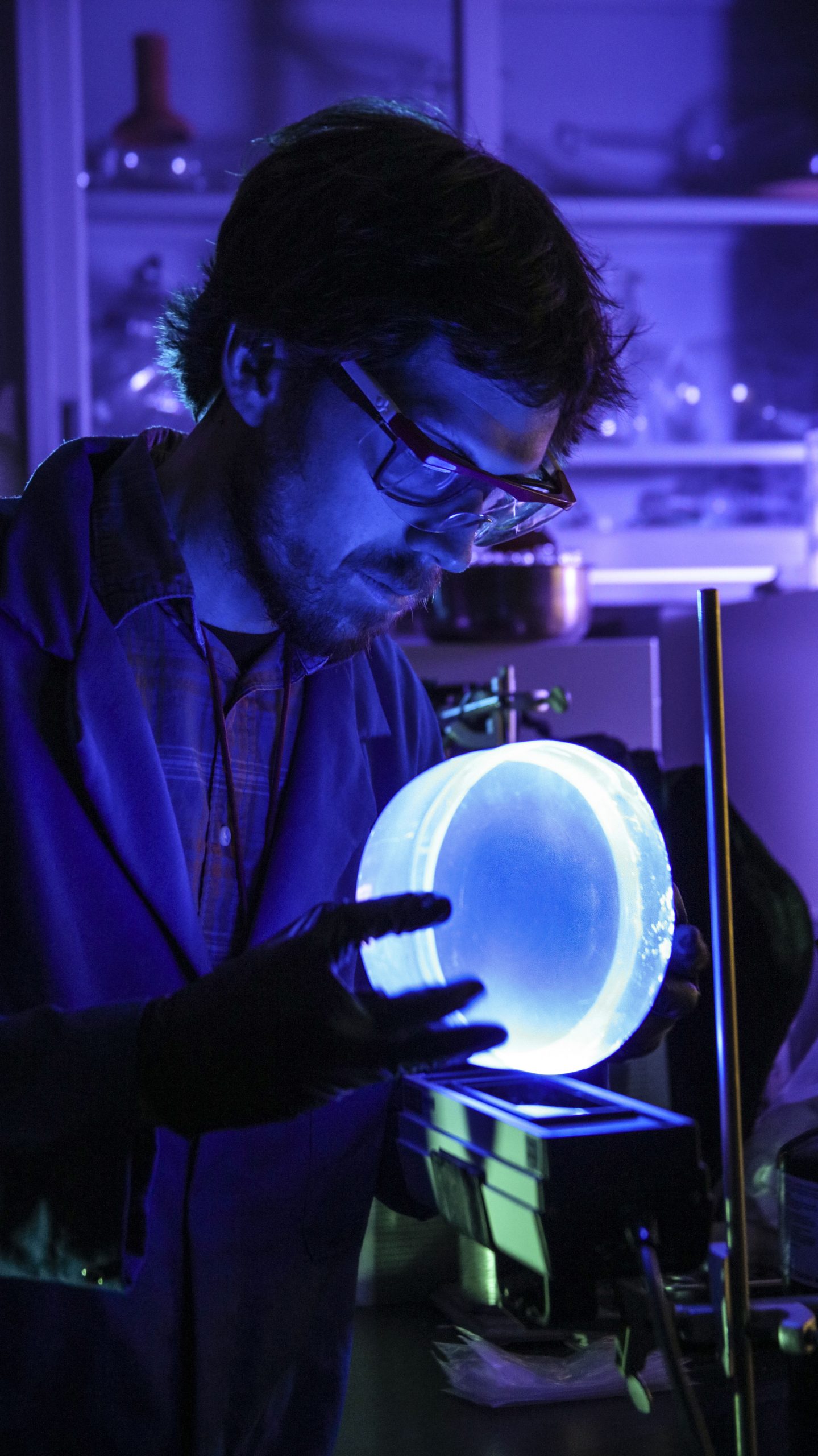
The change also fits well into existing manufacturing processes for the plastic, so manufacturers have been able to scale up production rapidly to make large sheets capable of replacing fogged detectors.
These radiation detectors are sheets of polyvinyltoluene (PVT) plastic, 2 inches thick and 6 to 8 feet high, deployed in traffic lanes at ports of entry. The detection component in the plastic is a fluorescent molecule that glows when radiation hits the material. Light collectors mounted on the top of the sheet gather light from the glowing molecules; the amount of light they register reflects the amount and energy of radiation that hit the material, the number of light particles coming from the fluorescent molecule and the efficiency of light transport through the plastic.
“For reliable radiation measurements, it’s of the utmost importance that the material is optically transparent and remains that way for decades,” Sandia materials scientist Nick Myllenbeck said.
However, analysts that use PVT noticed that the radiation detection performance of the plastic was starting to degrade after the plastic had spent a few years in the field. By eye, they saw what appeared to be fog droplets forming inside the material. These droplets scattered light from the glowing molecules and prevented some of the light from reaching the detectors, reducing the detector’s sensitivity over time.
Microscopy reveals fog source
To figure out how to prevent this fogging, Sandia researchers, working with colleagues at Lawrence Livermore, Pacific Northwest and Oak Ridge national laboratories, first needed to know how the fog formed. They suspected it appeared in the material much like it does in air — by water condensing as the air temperature drops overnight.
The researchers put small samples of the radiation-detecting PVT plastic in a humid chamber and cycled the temperature from warm to cool to mimic daytime and nighttime temperatures. The samples absorbed only about 0.03% water by mass, but during cooling cycles, the researchers saw the fog-like droplets appear in the material.
When they examined the material under an optical microscope, however, they realized the droplets were microscale defects in the plastic caused by condensed water absorbed from the air.
They eventually realized that the defects formed in two phases. During the first few warm and cool cycles, the fog-like defects appear to be completely reversible upon heating or drying out the plastic. However, if the water remains in the plastic and the material experiences enough temperature cycles, the defects grow and become permanent. Both defect types can adversely affect the performance of plastic scintillators in the field, Myllenbeck noted.
Non-fogging formula easy for manufacturers to produce at scale
Once the researchers knew how the fog formed, they hypothesized that they could add a chemical component to the plastic to keep water from forming defects inside. Materials scientists from Sandia and Lawrence Livermore, sharing funding from the Department of Homeland Security Countering Weapons of Mass Destruction Office, experimented with various additives to stabilize water by means of hydrogen bonding to the additive.
At Sandia, Myllenbeck and his colleagues started with the current PVT formula and added one ingredient: a commercially-available additive that can interact favorably both with water and the plastic matrix. When they tested the new material under accelerated temperature and humidity conditions, the researchers did not see any sign of fogging after tens of cycles. In contrast, the standard plastic would fog severely after just one cycle. Myllenbeck suspects that the water inside the plastic clings to the additive rather than to other water molecules, which prevents droplet formation, and thus light scattering defects.
“This one ingredient change is a huge advantage to manufacturers,” he said. “They only have to add a small amount of this compound to their existing formula, with minor process modifications, to produce a nonfogging material that performs identically to the existing plastic.”
As a demonstration of scalability, a property that had previously eluded the multi-lab team, a PVT manufacturer working with the multilab team has produced numerous 2/3-scale parts with the new formula. They plan in the next several months to make full-scale panels suitable for field deployment, Myllenbeck added.