ALBUQUERQUE, N.M. — Sandia National Laboratories is partnering with Flowserve Corp. and Kairos Power LLC on a $2.5 million, three-year Department of Energy Advanced Valve Project grant to lower the cost and boost the efficiency of concentrating solar power in the U.S.
Control valves are a critical link in managing the solar energy captured by next-generation concentrating solar power plants. They must safely and reliably collect, store and transfer extremely hot and corrosive chloride salt to be used for generating electricity for public use.
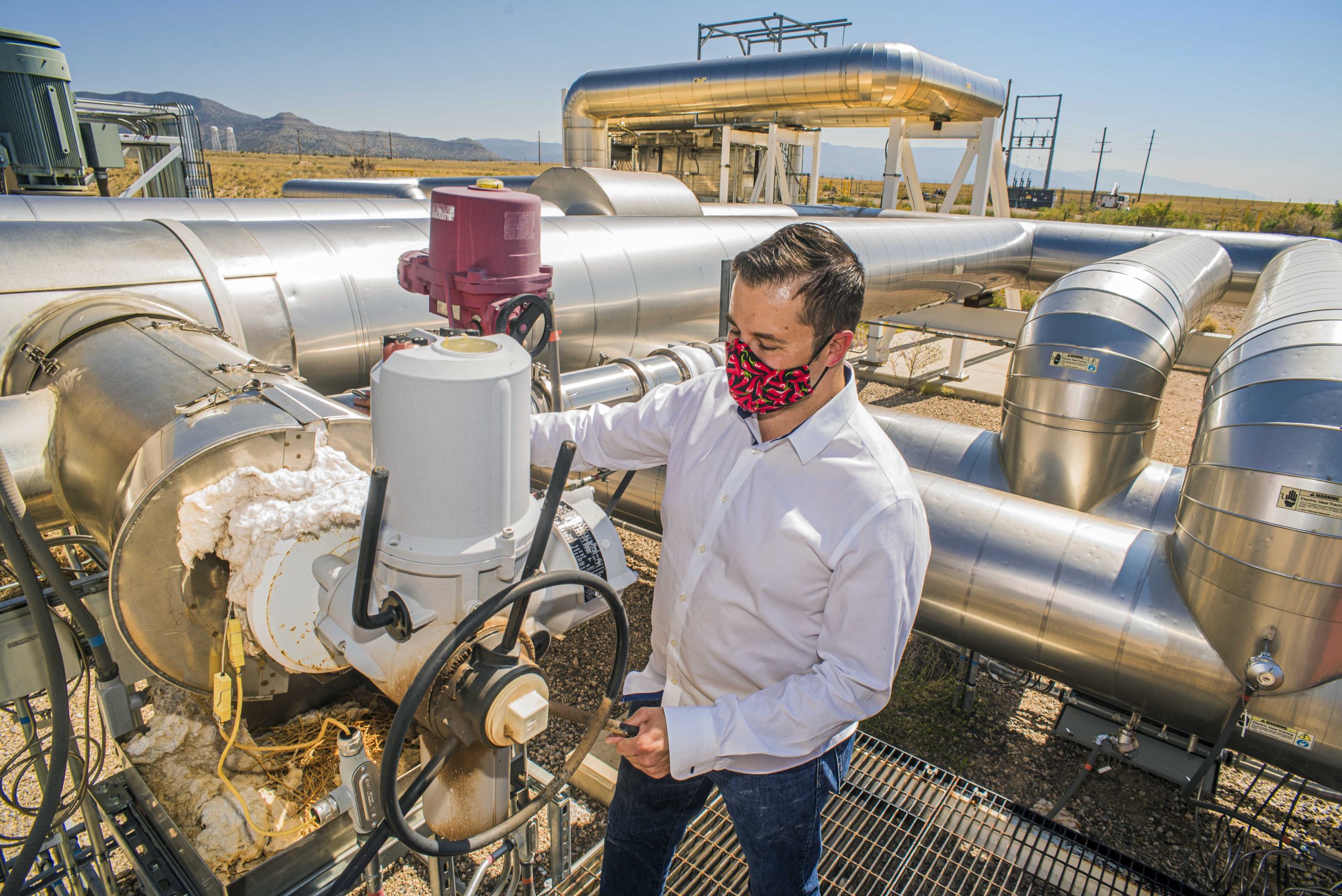
A vastly more reliable, higher-temperature molten salt valve is vital in achieving DOE SunShot targets that will significantly lower power-generating costs while increasing production. SunShot aims to reduce the total costs of solar energy, making it cost competitive at large scale with other forms of energy without subsidies by the end of the decade.
“We’re expecting to support significantly bringing down the concentrating solar power levelized cost of energy to 5 cents per kilowatt-hour, per DOE 2030 baseload targets,” said Ken Armijo, Sandia’s principal investigator on the project.
The project will investigate a newly designed molten salt valve as part of a complete solar energy management system. If successful, these redesigned valves also can be used for energy transfer in other fields, including nuclear energy and petrochemical industries.
Failing salt valves challenge system sustainability
Concentrating solar power systems must handle molten chloride salt temperatures that can reach in excess of 750 degrees Celsius, or nearly 1,400 degrees Fahrenheit.
Concentrating solar power and other energy sources super-heat liquid, which is then pumped through a network of pipes and transported to the power station to generate electricity. Molten salt is the preferred liquid for delivering and storing lava-hot liquid energy because it retains its viscosity, as opposed to water, which converts to steam under such extreme temperatures. Molten salt also provides a more consistent temperature throughout the power plant during energy collection and delivery.
Proportional flow-control valves serve as the piping-system gatekeepers for delivering this harvested energy to the production side of a power plant. These valves are continually confronted with extreme temperatures, pressures and flow rates, and oftentimes, extraordinarily low outdoor temperatures. Valve freezing and thawing due to the vagaries of weather can create expanding and contracting materials resulting in weaknesses in the system, Armijo said.
“Molten salt flow valves must maintain constant heat transfer and fluid flow, despite severe temperature variabilities,” he said.
As concentrating solar power plants become increasingly larger and more productive, system components like flow-control valves must withstand even more extreme conditions to perform reliably.
“As we go to higher temperatures in these systems, there’s a penalty we pay with thermal expansion,” Armijo said. “Under extreme heat and pressure, materials and components can swell, bend and warp.”
Current molten salt valves require expensive, frequent maintenance, according to Armijo. But perhaps a bigger challenge is that molten salt valve failures can occur frequently throughout the system, resulting in expensive downtime to repair or replace the valve and repack and replace the seals.
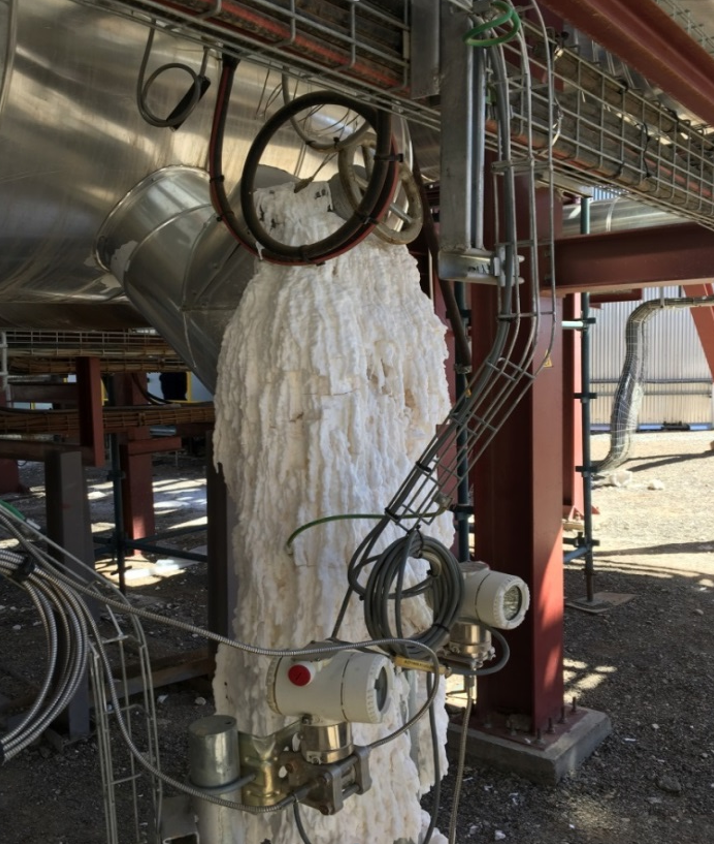
Add the corrosive properties of salt, and you have a recipe for repeated breakdowns. If a valve failure is happening on a monthly basis in systems with between 10 and 15 valves, the system can be inoperable for days, weeks or even months. The associated loss of revenue can render these systems unsustainable.
New materials, design create a stronger valve
Today’s molten salt valves are formed with expensive chromium-based materials that are susceptible to corrosion, and high nickel-based materials generally do not have the strength at these high temperatures. Sandia will focus on developing less expensive base materials for the valve and adding a durable clad composite overlay to withstand corrosion, increasing durability while significantly reducing manufacturing costs.
In addition to the materials upgrade, innovative trim design elements would automatically buffer pressure surges and pulses as molten salt passes through, while dissipating heat to avoid valve damage. The new design also would enable use of reformulated packing materials to create a modular quick-change system for replacing costly bellow seals, which can rupture if activated with frozen salt present, Armijo said.
Another major valve reliability issue is internal salt freezing from low outdoor temperatures, which can cause mechanical stress on valve stems, seals and bonnets. An innovative feature within the valve should address this freezing issue by carrying heat through the valve stem to the packing area, thus maintaining a constant internal temperature and reducing operations and maintenance, he said.
“It’s the temperature differences along the valve that can cause leaking problems with gaskets and seals,” Armijo said.
The self-contained thermal management system is expected to reduce material stress and fatigue that can rupture pipe and valve systems and improve component longevity. “We’ll fine-tune controls to keep the valves at a uniform temperature,” he said.
The advanced valve design also will employ innovative gaskets, seals and packing to reduce maintenance demands. “And, the new design can include pressure and flow sensors on the valves themselves, which will reduce the cost of having to add pressure and flow sensors throughout the system,” Armijo said.
This self-contained, integrated thermal management system should dramatically reduce the levelized cost of electricity — the cost of the system divided by lifetime energy output — which has become increasingly competitive for developers to win solar projects.
These performance upgrades also will address the DOE’s Generation 3 Concentrating Solar Power Systems program, which calls for advancing high-temperature concentrating solar power components and developing designs with thermal energy storage that can reach high operating temperatures.
Powerhouse partnership integrates strengths
The partnership, with decades of experience in researching and developing molten salt systems, will examine new control-valve materials, design and modular features to withstand extreme temperatures and pressures associated with costly valve failures.
Sandia has more than 40 years of experience in research and development for advanced concentrating solar power systems and components, particularly for molten salt technology. The labs will test potential materials using a chloride-salt blend within its chemistry laboratories. The valves will be evaluated for their corrosion resistance, material loss and mechanical strength under several scenarios at Sandia’s National Solar Thermal Test Facility.
“Sandia Labs has been known for materials research for more than 70 years,” Armijo said. “We can perform very high temperature new-material tests for ceramics, metal alloys and composite materials. Very few facilities in the world can do this.”
Flowserve Corp. has experience in analytical methods for high-temperature and high-pressure fluids, and system evaluation for molten salt applications globally. The company will develop two competing stem-sealing systems, comparing a bellows design with a quick-change packing canister design. Both designs could potentially use the self-contained thermal management system.
Kairos Power LLC will construct an isothermal-batch flow-valve test system to investigate valve performance and reliability up to a 750 degrees Celsius operational temperature. Kairos also will perform reliability assessments on the prototype 2-inch valve and lead valve validation experiments at its facility.
Sandia will coordinate all research and development efforts for the project.
Ultimately, this project should help make solar energy generation more affordable by decreasing flow-valve cost using less expensive materials, eliminating the need for multiple sensors on the system and reducing maintenance and repair downtime, Armijo said.